Solutions beyond tomorrow already today
"Solutions beyond tomorrow" - with this claim and the associated target image, Krones is taking a very clear path into the future. It's about tackling three of humanity's greatest challenges together: climate change, feeding the world's population, and responsible use of packaging materials.
These ambitious goals require innovative solutions that "go beyond tomorrow". Solutions that benefit humanity and our planet sustainably and in the long term. But solutions that also contribute to our customers' goals. In order to pursue this goal in a targeted manner, Krones' innovation work starts with the consumption of resources, with the reduction of waste and emissions, but also with the performance of our customers' production.
Customised complete lines for individual requirements
Best product quality, lowest energy and resource consumption, highest system performance - every beverage producer strives to get the most out of their production. Krones is the ideal partner for this. This is because our decades of expertise in machine and plant engineering, coupled with strong innovative strength, offer the ideal conditions for creating the perfect individual line concept for every customer.
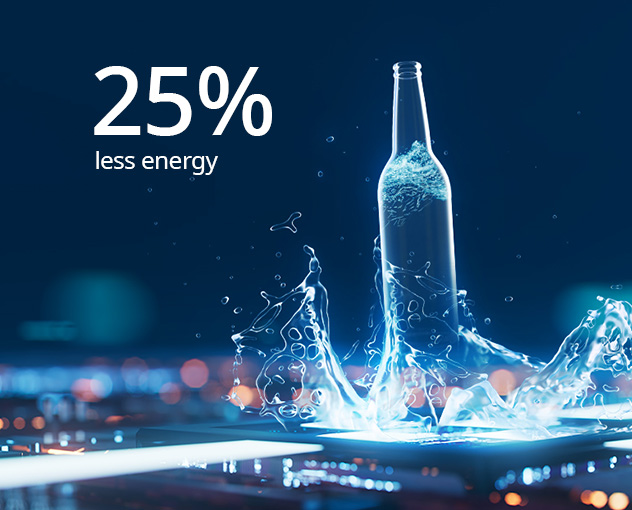
With the current development project for the Modulfill HES, Krones ushers a new era in filling beer and CSD. For example, a combination of a redesigned filling valve and dry-running vacuum pump ensures the best values for oxygen pick-up and CO2 consumption and reduces energy consumption by up to 25 percent. Automated probe adjustment and CIP cups also reduce the need for manual intervention, thereby increasing production time and OEE.
With the current development project for the Modulfill HES, Krones ushers a new era in filling beer and CSD. For example, a combination of a redesigned filling valve and dry-running vacuum pump ensures the best values for oxygen pick-up and CO2 consumption and reduces energy consumption by up to 25 percent. Automated probe adjustment and CIP cups also reduce the need for manual intervention, thereby increasing production time and OEE.
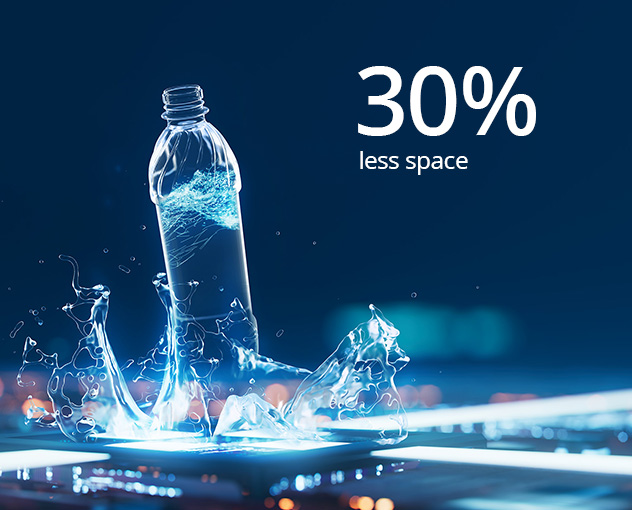
With an incredible 100,000 containers per hour, the latest version of the ErgoBloc L sets new speed records. To make this performance possible, the line is operated with a sophisticated system consisting of the Contiform blow moulder, an Ergomodul labeller specially optimised for this performance and a Modulfill Dual with two filling and capping carrousels. Thanks to this clever combination, the ErgoBloc L requires around 30 percent less space than conventional block solutions and compared to individual machines even 70 percent less.
With an incredible 100,000 containers per hour, the latest version of the ErgoBloc L sets new speed records. To make this performance possible, the line is operated with a sophisticated system consisting of the Contiform blow moulder, an Ergomodul labeller specially optimised for this performance and a Modulfill Dual with two filling and capping carrousels. Thanks to this clever combination, the ErgoBloc L requires around 30 percent less space than conventional block solutions and compared to individual machines even 70 percent less.
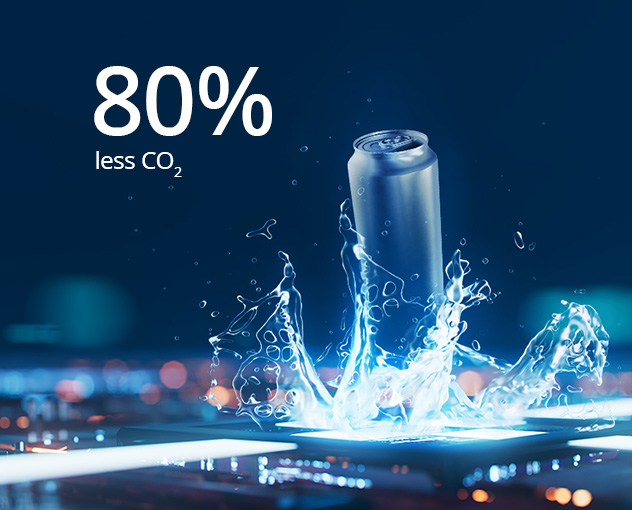
With the sustainable LitePac Top Protect secondary packaging, 80 percent of CO₂ can be saved compared to conventional shrink-wrapped packs. And the best thing is: The solution can also be retrofitted in most cases in existing lines without having to compromise. With a speed of up to 108,000 cans per hour, the Variopac Pro handles LitePac Top cartons just as fast as other conventional types of packaging.
With the sustainable LitePac Top Protect secondary packaging, 80 percent of CO₂ can be saved compared to conventional shrink-wrapped packs. And the best thing is: The solution can also be retrofitted in most cases in existing lines without having to compromise. With a speed of up to 108,000 cans per hour, the Variopac Pro handles LitePac Top cartons just as fast as other conventional types of packaging.
Process technology of the Krones Group for beverages, liquid food and new food
Sustainability not only plays a key role in the filling and packing technology sector. In product manufacture there are a number of options available for saving water, energy or media. And the process technology experts from the Krones Group have dedicated themselves to the task of discovering exactly what opportunities are available and then translating them into suitable solutions.
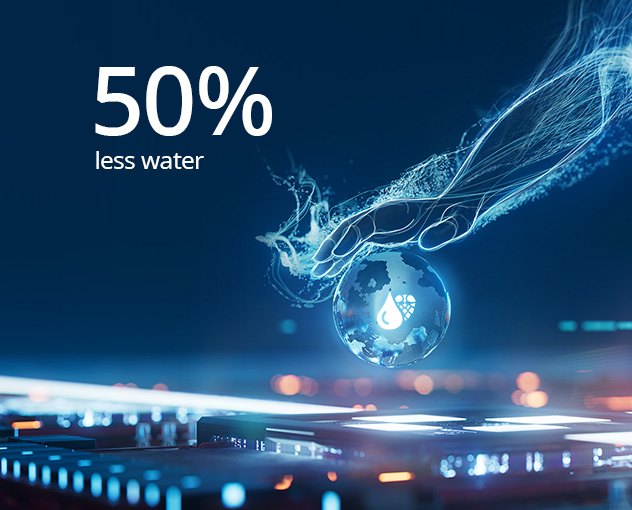
The Brewnomic concept comprises numerous modules in order to achieve a CO₂-neutral and energy self-sufficient brewing process. Now Steinecker offers three new options for even more sustainable brewing: With the Phoenix BMC system, residual materials can be upcycled and used for energy recovery. A Water Sustainability Concept reduces the water consumption by up to 50 percent. And the integration of an in-house CO₂ recovery system makes breweries independent of current market conditions and increases the sustainability of the production process.
The Brewnomic concept comprises numerous modules in order to achieve a CO₂-neutral and energy self-sufficient brewing process. Now Steinecker offers three new options for even more sustainable brewing: With the Phoenix BMC system, residual materials can be upcycled and used for energy recovery. A Water Sustainability Concept reduces the water consumption by up to 50 percent. And the integration of an in-house CO₂ recovery system makes breweries independent of current market conditions and increases the sustainability of the production process.
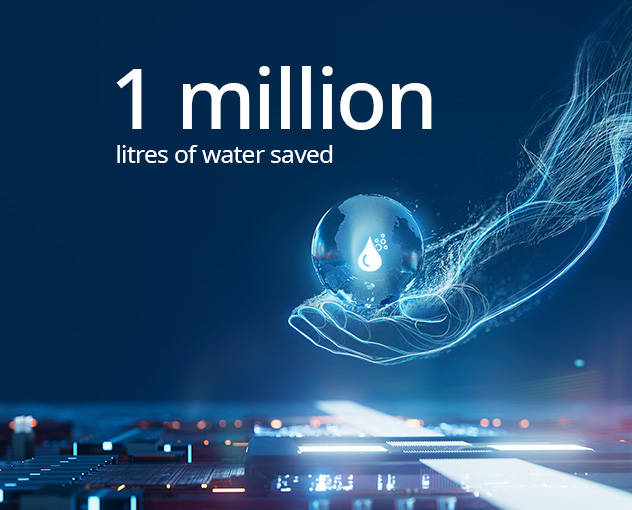
Krones presents the Contiflow beverage mixing system with various new features that are particularly impressive in terms of production efficiency: An integrated syrup feed tank minimises product losses and is particularly useful when the line and syrup room are not installed directly next to each other. The high-end version includes a concept with two tanks, which also significantly reduces changeover times. Other optional features also ensure savings in CO₂ and water: For example, with a production time of 16 hours a day and 250 days a year, over one million litres of water can be saved.
Krones presents the Contiflow beverage mixing system with various new features that are particularly impressive in terms of production efficiency: An integrated syrup feed tank minimises product losses and is particularly useful when the line and syrup room are not installed directly next to each other. The high-end version includes a concept with two tanks, which also significantly reduces changeover times. Other optional features also ensure savings in CO₂ and water: For example, with a production time of 16 hours a day and 250 days a year, over one million litres of water can be saved.
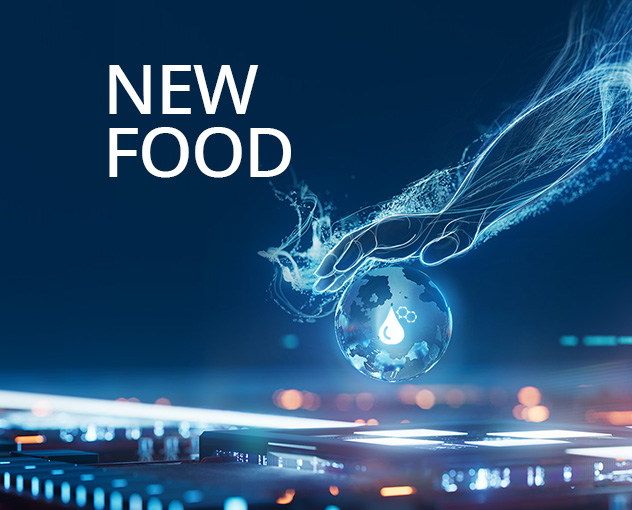
Take a bioreactor that works on the basis of a circulation unit, fill it with microorganisms and initiate the process of precision fermentation - and the result is proteins that serve as the basis for meat substitutes or other food alternatives. Admittedly, it's not quite as simple as it sounds. This is where Steinecker's team of experts comes into play, using its extensive experience in brewing and process technology to work with interested customers to turn their visions of New Food into reality.
Take a bioreactor that works on the basis of a circulation unit, fill it with microorganisms and initiate the process of precision fermentation - and the result is proteins that serve as the basis for meat substitutes or other food alternatives. Admittedly, it's not quite as simple as it sounds. This is where Steinecker's team of experts comes into play, using its extensive experience in brewing and process technology to work with interested customers to turn their visions of New Food into reality.
Performance boost thanks to digital solutions
An important keystone of our innovation work is digitalization - because digital updates help to make our machines even more efficient and economical.
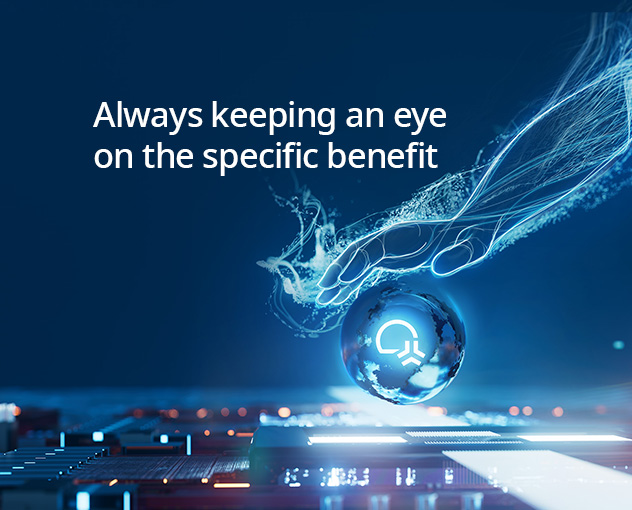
Our Digital Services offer a holistic approach to digitalization. This is because they are tailored precisely to the respective challenges and pain points of our customers. The most recent example is Shopfloor Guidance. The solution recognises when the machine status changes, immediately informs the operating personnel and immediately initiates actions to counteract a standstill.
Our Digital Services offer a holistic approach to digitalization. This is because they are tailored precisely to the respective challenges and pain points of our customers. The most recent example is Shopfloor Guidance. The solution recognises when the machine status changes, immediately informs the operating personnel and immediately initiates actions to counteract a standstill.
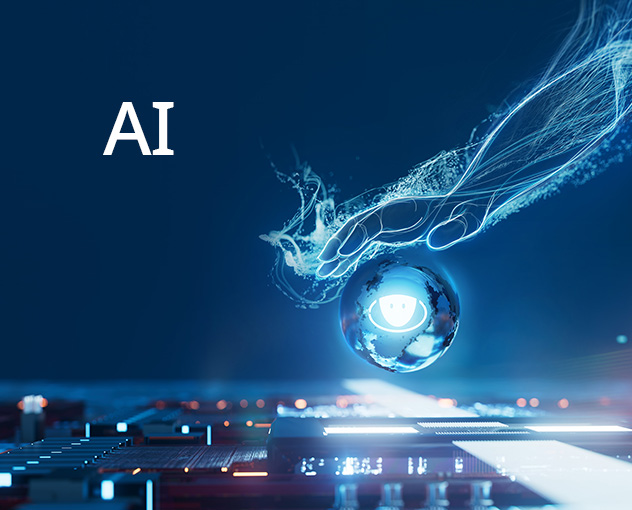
There is also a lot of digitalization in our machines and systems themselves - namely in the form of artificial intelligence. This enables decisive data-based improvements to be made to both the Contiform stretch blow moulder and the Linatronic AI empty bottle inspector, for example.
There is also a lot of digitalization in our machines and systems themselves - namely in the form of artificial intelligence. This enables decisive data-based improvements to be made to both the Contiform stretch blow moulder and the Linatronic AI empty bottle inspector, for example.