The block solution for the high-performance range
A lot of machinery in just a small space
When it comes to output per square metre, the ErgoBloc L is in a league of its own. The wet section block has an output of up to 100,000 containers per hour – and requires 30 percent less space than conventional block solutions.
At a glance
- Functions: Stretch blow moulding, labelling, filling and capping
- Output: up to 100,000 containers per hour*
- Processing range:
- Non-carbonated and carbonated beverages
- Cylindrical and square PET containers
- Standard and lightweight containers
- Container volumes of 0.25 to 3.5 litres
- Containers of up to 100 percent rPET
- Self-adhesive labels and reel-fed plastic labels
- Flat caps and sports caps
*depending on the processing range
L = Liquid
Functions and structure

- Labelling station with selective labelling for up to 50,000 containers per hour
- Container base cooling only required with CSD
Maximum output in the smallest space
100,000 containers per hour – utmost efficiency on the market!
Overview of processing range
- Non-carbonated beverages
- Cylindrical PET containers
- Containers of up to 100 percent rPET
- Standard and lightweight containers
- Volumes of up to 0.75 litres
- Plastic reel-fed labels
- Flat caps
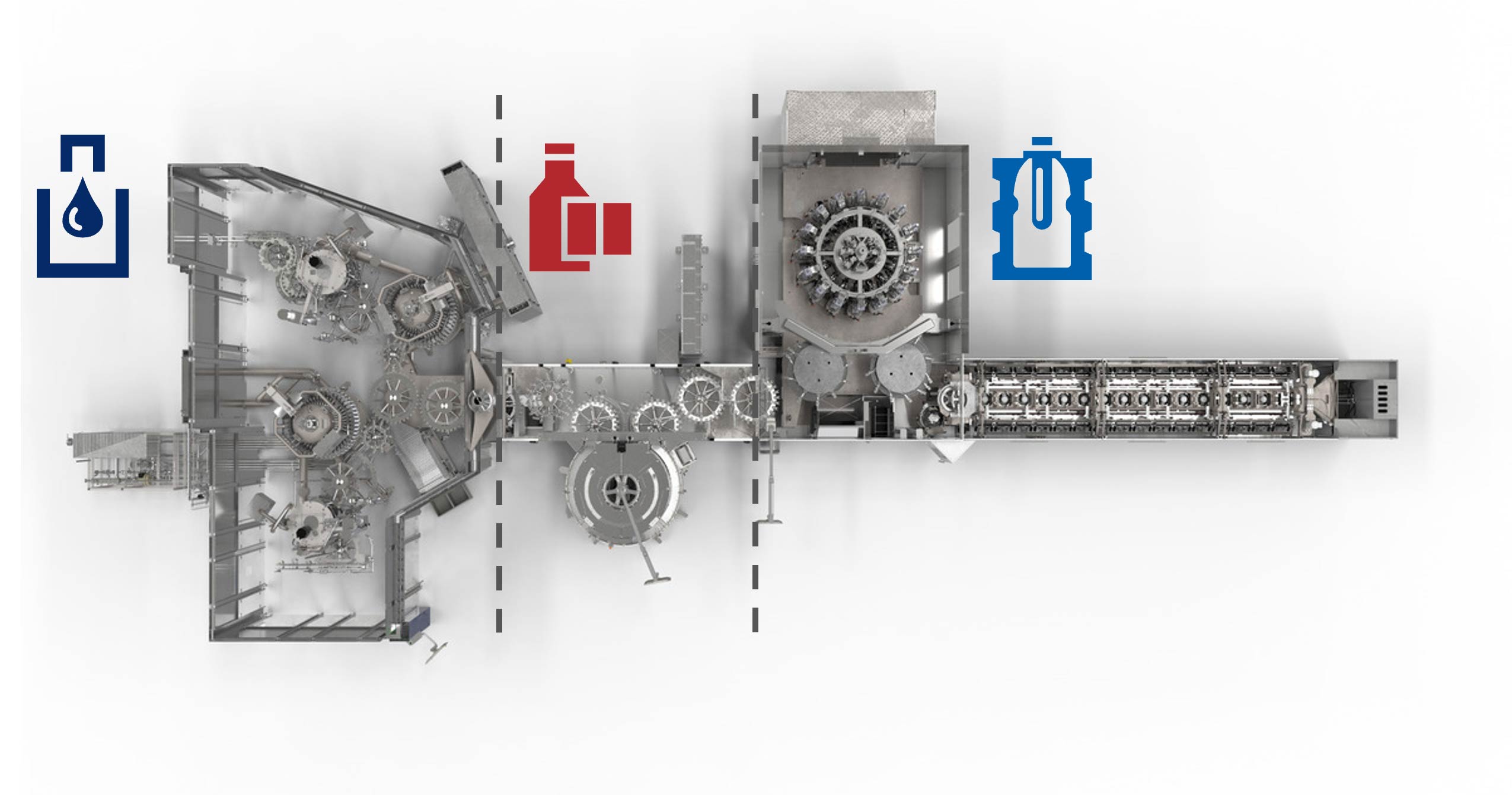
- Up to 2,750 containers per hour and blowing station
- Up to 30 percent* less compressed air consumption due to Air Wizard Triple
- Up to 5 percent* reduced energy consumption of the infrared oven
- Maximal line OEE due to "Skip-and-Run"
*in comparison to Contiform 3
- "No bottle – no label" function
- Minimal glue consumption (Contiroll TS)
- Best precision due to neck-handling system
- Minimal label tension due to gentle, dynamic buffering
- Optimised glue steam extraction system
- Infinitely variable filling speed
- Cap sorting close to the ground with maximum speed
- Up to 40 percent* less filling valves
- Up to 10 percent* less space requirement
*in comparison to conventional fillers
Your benefits
Four process steps – one operator
With the ErgoBloc L, the entire process from stretch blow moulding right through to the capping of the containers can be handled by just one person. The compact design without conveyor sections also keeps the transport distances short and offers an easy overview over the entire line.
Large output in a small area
Even though it processes up to 100,000 containers per hour, the ErgoBloc L requires up to 70 percent less space than a line consisting of individual machines. This way, you can save hundreds of square metres of hall surface.
Trouble-free continuous operation
Full power without breaks: The labelling module automatically detects bottle gaps and does not apply glue or labels in this case. Disruptions due to missing bottles and unnecessary glue and label consumption are therefore not an issue.
Energy savings
From optimised infrared heating technology to consistently implemented servo drive technology: The topic of energy efficiency goes all the way through the block just like a red thread. Particularly ambitious savings targets can also be achieved with the Air Wizard Triple compressed air recycling system.
Gentle treatment for PET containers
The active transfer grippers only touch the preforms and bottles in their neck area. This makes the contact area between the material and the machines as small as possible and minimises the risk of damage.
This is why the ErgoBloc L is enviro-classified:
Energy efficiency
- Increased station performance during stretch blow moulding and labelling
- Reduced energy consumption thanks to the omission of transfer starwheels and redundant components
- Height-adjustable base thermal shield and frequency-controlled neck finish cooling system
- Energy-efficient separated vacuum during labelling
Media efficiency
- Efficient cooling of the entire block
- Air Wizard Triple air recovery system
- No compressed-air consumption during the filling process
Environmental compatibility
- Use of enviro-compliant lubricants
- Recoverable CIP media
This product is enviro classified
Top technology for ecologically efficient production
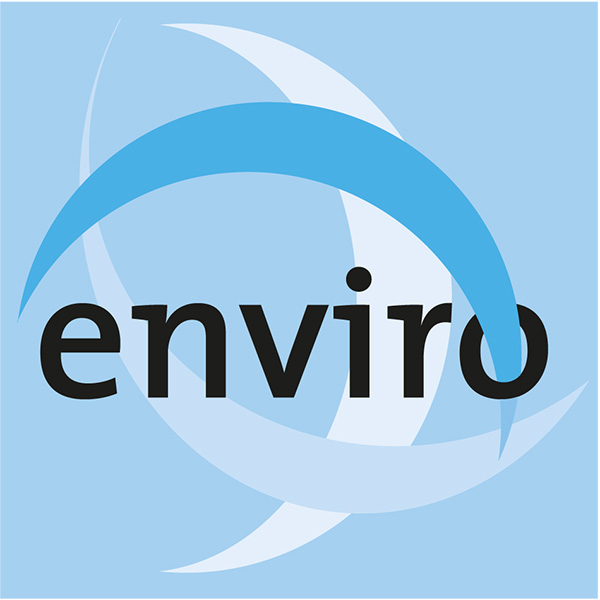
The Krones sustainability programme enviro: top technology for ecologically efficient production.