Complete concept for waste water recycling
Recycling waste water to new process water
A considerable amount of waste water is generated during production – between one and three litres per litre of beer or soft drink and two litres per kilo of PET. This is exactly the reason why not only beverage and liquid-food producers but also recyclers are constantly looking for solutions to reduce this waste water volume. Krones has therefore developed the HydroCircle – a concept for recycling production waste water to new process water. All process steps that produce waste water during production are taken into account.
At a glance
- Recycling of waste water into process water
- Up to 80 percent lower water consumption during production
- Closed loop concept under consideration of the entire process chain
- Use of proven plant technology such as Krones Hydronomic and patented fully biological waste-water treatment technology
- For beverage and liquid food producers as well as for recycler
Variant 1: Closed circle concept for treating brewery waste water
With the HydroCircle system, waste water from production is treated to produce new process water. All process steps that produce waste water during production are taken into account.
The biological contaminants contained in waste water must first be cleaned before it can be reused. Here, Krones uses a patented solution that guarantees high process stability.
At the heart of this technology is a unique down-draft reactor, in which the waste water is sprayed through nozzles mounted on the roof and then sinks. In the process, it migrates through anaerobic biomass, which is located in so-called carriers, i.e. biofilm carriers. The methane-enriched biogas produced in the upper part of the reactor immediately rises to the top, while water and sludge sink to the bottom and leave the reactor separately. Thanks to this downdraft technology, the chemical oxygen demand (COD) can be reduced by up to 90 percent anaerobically within a short period of time.
The carriers are characterised by a particularly open structure which prevents blocking and allows high material conversion rates to be achieved.
Water – as pure as it gets
The Hydronomic RO module serves to desalinate water down to a usual residual content of less than three percent.
- Tangential flushing of a semi-permeable membrane with untreated water
- Discharge of the permeate to a central collecting pipe
- Flushing with permeate to prevent scaling and biofouling
The components
- Consecutive switching of several spiral modules (stage configuration) for graduated concentrate treatment
- Separation of the spirally-wound membrane surface via mesh spacer
Efficiency in figures
- Permeate output: up to 120 m³/h
- Yield: approx. 70 % (on the basis of the respective initial CO2 content)
Once reprocessed, process water can be reused at numerous points of production:
- at the cooling tower
- CIP plant
- as boiler feed water
- at the washer
- at the pack washer
- at the rinser
- as grey water
The waste water treatment system can be used not only for the integration of new factories, but also for retrofitting existing factories. The only prerequisites are: Waste water streams should already differentiate between process water and other water and there should be sufficient space for the required tanks and utilities.
Variant 2: Closed circle concept for processing waste water of recycling systems
From waste water to process water in the plastic recycling process
Treatment step 1
Waste water from the recycling process contains suspended solids, among other things. These are removed with the help of dissolved air flotation (DAF). For this purpose, the suspended solids contained in the waste water are transported to the water surface through adhering gas bubbles while air is supplied. They are then removed from the water surface with an appropriate clearing device.
The solids removed from the water surface are fed into a sludge retention tank. From there, the sludge goes to a decanter centrifuge for dewatering. The waste water from this centrifuge is fed back into the DAF unit and the dewatered sludge is collected and disposed of.
Treatment step 2
In order to achieve the fresh-water quality, a second treatment step is necessary. Impurities, such as heavy metals, microplastics or organic compounds, are removed from the liquid phase by means of the membrane bioreactor.
Optionally, the membrane bioreactor can be followed by reverse osmosis, for example using the Hydronomic RO.
Possible uses of waste water treatment in plastics recycling
In plastics recycling, the process water can be reused in various places:
- Grinder water
- Wash water in the water cascade
By using the HydroCircle technology, you will...
- save large quantities of fresh water in plastics recycling.
- remove large amounts of microplastics in the water.
Thus, only a minimal discharge into the municipal sewage systems is required. The dewatered sludge is sent to a sewage sludge incineration plant.
The HydroCircle technology is a very robust and low-maintenance system with low operating costs and worldwide service and training support.
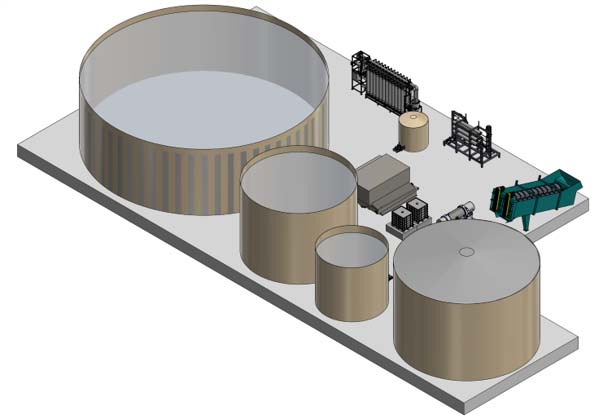
Your benefits
New installation or retrofitting
This system can be used not only in the integration of new factories, but also for retrofitting existing factories.
Significant savings in water
Thanks to HydroCircle, up to 80 percent less water is required for production - which naturally has a noticeable effect on both water costs and the company's environmental balance.
Tried-and-tested technology
Krones relies on proven technology for its concept: Thus the system for waste water treatment comes from an experienced partner. Krones provides the Hydronomic system for water treatment.
High hygienic standard (only applies to the closed circle concept for treating brewery waste water)
The Hydronomic systems are completely designed of stainless steel. They can therefore be completely sanitised with hot water
The whole factory at a glance
The concept takes into account all process steps that produce waste water during production. In this way, the volume of waste water can be significantly reduced throughout the entire production process.