But do you know exactly what lies behind the term injection moulding? In the following article, you will get a brief introduction to the subject – and learn why the acquisition plays an important role for Krones, in two respects.
What is injection moulding?
In simple terms, the injection moulding process is where granules, made from plastic, for instance, are heated to 200 to 300 degrees Celsius, which liquefies them. In the next step this mass is injected under pressure into what is known as the injection mould. Since the mould, at about 20 to 120 degrees Celsius, is significantly colder than the mass injected into it, the molten material cools down inside it and hardens. Because of the heat lost as it cools down, however, the mass shrinks. This shrinkage is compensated by squeezing in more material. On completion of the injection moulding process, the mould is opened and the manufactured product either falls into a collecting container as bulk material or is removed by handling tools.
Not only are preforms manufactured in this way, but so too are caps, plastic containers for margarine and yoghurt, for instance, as well as Petri dishes and pipette tips for medical applications.
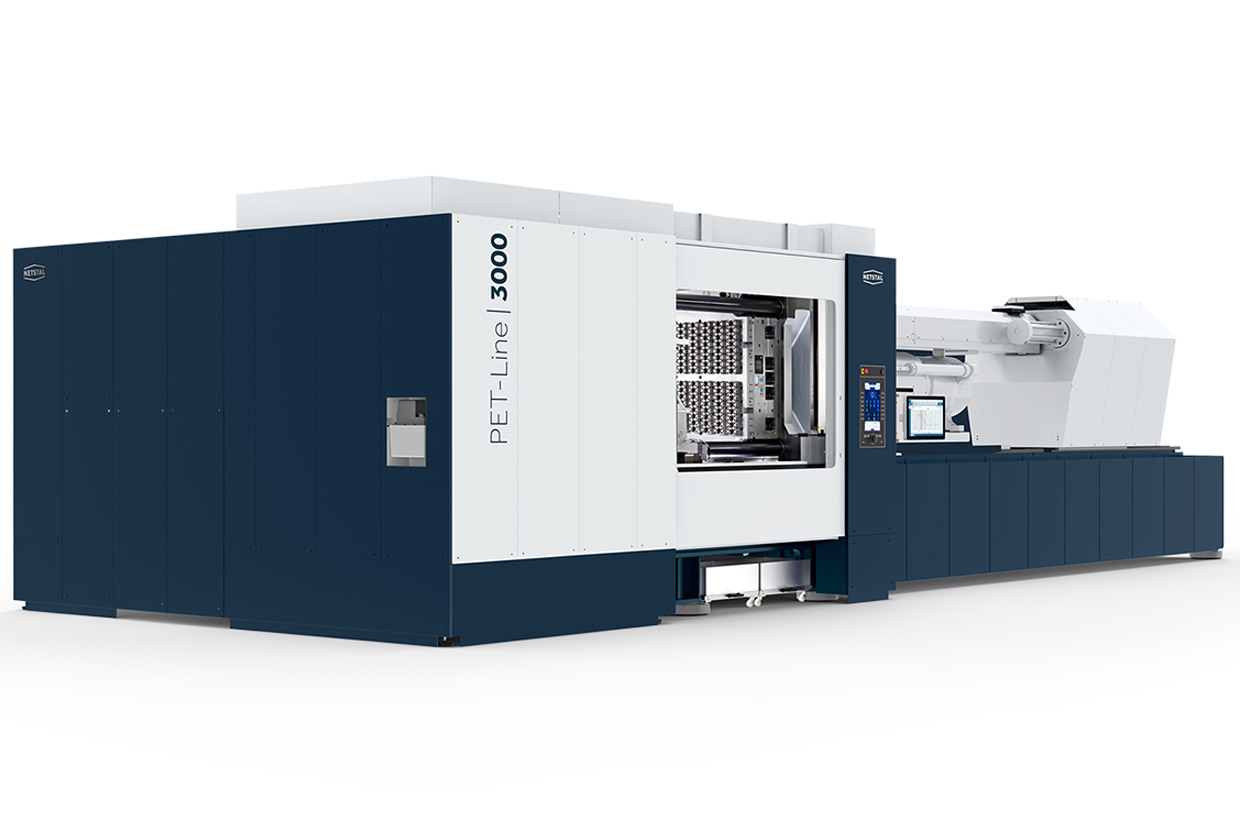