It’s Monday morning, six o’clock, and the early shift is starting work at Erdinger Weissbräu. The bottling foreman releases the first production order of the day in the Line Management system, thus sending all necessary information and parameters to the respective machines. At the same moment, a machine operator at the repacking line is setting up the labeler for the new bottle type. The Line Management system has already made all of the settings for the new order and, in parallel, requested the appropriate supplies. A signal goes to the warehouse management system, indicating which bottles are needed on the line. The requisite labels and cartons are shown on the machine’s display. The operator presses Start, goes to the carton erector and pushes the “Infeed clear” button. Now she has time to perform the changeover while the first bottles are already entering on the buffer conveyor. Step by step, the operator changes over each of the machines in the line.
Breweries with complex processes, like those at Erdinger Weissbräu, can benefit from Krones’ digital solutions. These tools take care of setting parameters on the machines and also monitor and optimize the filling processes. In Erding, Krones has integrated its solutions into several lines as part of a comprehensive multi-year IT project. The brewery has not only gone digital with its processes. It’s also streamlined its system environment and implemented SAP.
Erdinger Weissbräu
Beer from Erdinger Weissbräu is enjoyed in more than 100 countries around the world. But each individual bottle is brewed and filled right here in Erding, the brewery’s first and only production plant. Despite its increasingly international reach, the company remains true to its roots in Bavaria and to the traditional craft of brewing. The privately owned brewery was established in 1886. Today, it is the largest family-owned wheat-beer brewery in Germany. Up to 165,000 bottles are filled here per hour. The brewery is most well known for its Erdinger Weissbier, a wheat beer with fine yeast. Since 2011, it is also the top maker of non-alcoholic wheat beers on the market. Erdinger Weissbräu is demonstrating its adaptability without compromising its identity – and the same goes for the digital transformation of the brewery itself.
Many products means many changeovers
Changeovers like these are a regular occurrence at Erdinger Weissbräu since the company produces eleven different wheat beers and two pale lagers (“Helles”) in a variety of bottle types and sizes and with different labels to boot. In all, they handle more than 450 articles, which makes for a highly complex production and filling operation. In the past, that meant the machine operators had to fetch the right materials and bring them to the right line at the right time and then set the machine parameters individually for each order. It was a process that was prone to error. And so, the company wanted to automate the filling operation, with digital tools.
Wanted: lean, digital processes
Therefore, in 2015, Erdinger Weissbräu launched a comprehensive IT project that also involved streamlining the system environment since the existing IT infrastructure, which had grown rather organically over the years, contained more than 40 different digital systems and applications. One of Erdinger’s top priorities was to reduce the number of manual interventions – and, thus, the risk of error. Another was to have fast, succinct reporting. All in all, the goal was to increase efficiency. To achieve this, Erdinger Weissbräu turned to Krones, whose digital innovation team recommended three solutions that met these very needs: Line Management, Line Diagnostics and Manufacturing Intelligence.
Machines and digital services from a single source
It didn’t take long for the company to make the decision to implement these solutions from Krones. Since most of the equipment in the plant came from Krones, it made sense to use the industry leader’s corresponding digital services as well. With them, Erdinger Weissbräu gets a complete solution from a single source. “We’ve got many years’ worth of IT expertise in both greenfield and brownfield projects, and our solutions are unique in their depth of automation,” says Timo Frankl, Head of Sales Global Digitalisation and Digital Services at Krones.
We’ve got many years’ worth of IT expertise in both greenfield and brownfield projects, and our solutions are unique in their depth of automation.
Timo FranklHead of Sales Global Digitalization and Digital Services at Krones
Krones’ task, then, was to implement the digital solutions and establish efficient interfaces. That was accomplished in stages over the course of several years since Erdinger Weissbräu was, at the same time, switching over its system environment and implementing SAP. Three glass lines, a kegging line, two repacking lines and the sorting center, which acts as the hub for supplying all lines, were integrated. The comprehensive IT project began in 2015 with an update to the machines and digital technologies for the filling operation. In 2018, implementation and company-wide connection of the SAP systems started. The project was completed in 2022.
Integration of
1 glass line for returnable and non-returnable containers (52,000 bottles per hour)
2 returnable-glass lines (each rated at 52,000 bottles per hour)
1 kegging line (120 kegs per hour)
1 repacking line for cartons (38,000 bottles per hour)
1 repacking line for 11-bottle crates (4,500 crates per hour)
Sorting center which acts as the hub for supplying all lines
Line management: Everything under control, digitally
Krones Line Management is now at the heart of all the digitalized processes. The system manages all filling orders along the lines, directly matching the machine parameters to the respective orders. The sorting center for empty containers and crates is likewise connected to the digital solution. There, Line Management knows how many foreign crates and bottles have been rejected and how much new bulk glass must be fed and brought to the line for each order. That means the machine operators only have to handle the physical changeover of handling parts.
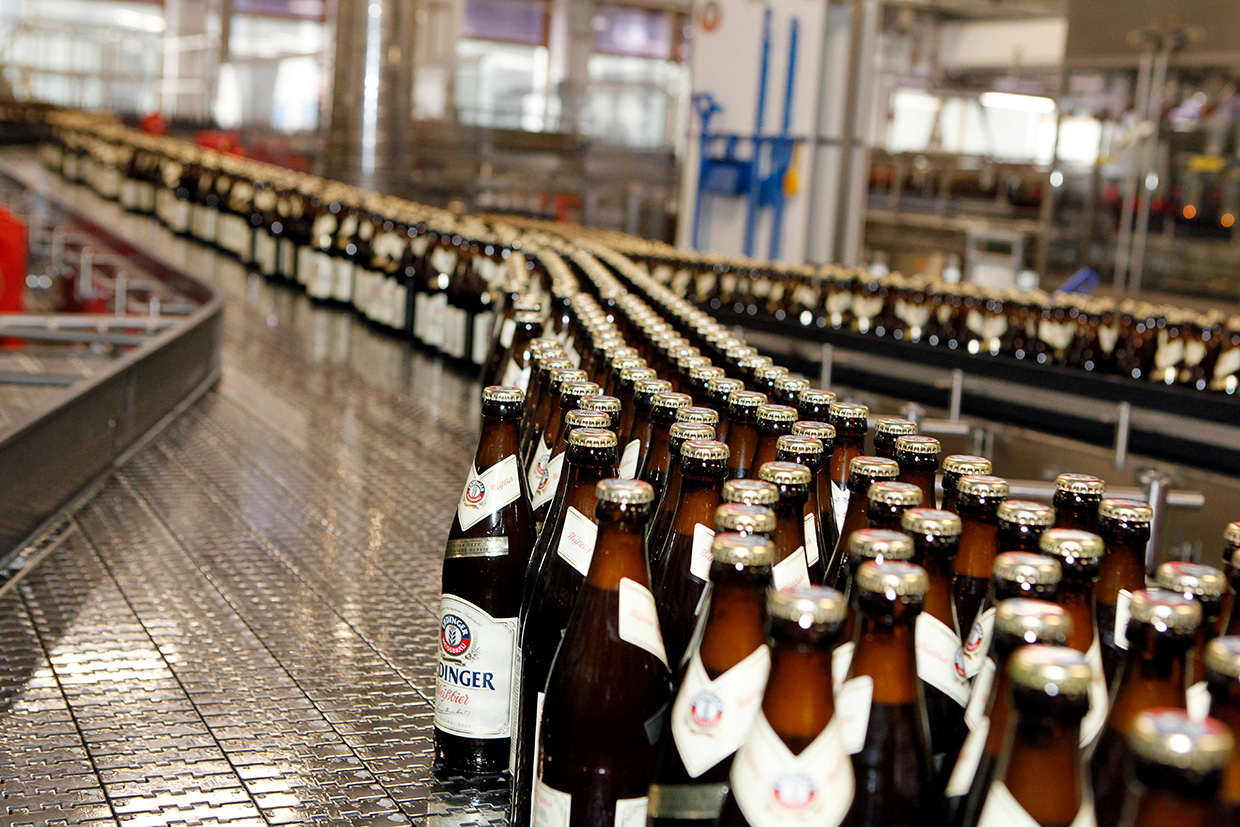
Erdinger Weissbräu
Line Management also supplies other areas such as labelling. The underlying system here is highly complex: The Weissbier with fine yeast alone can use 25 different back labels depending on the specific beer and the country to which it will be exported. Line Management knows which article is to be produced and its bill of materials and ensures that the right labels are used every time. Line Management transmits the specific characteristics of each label to the Checkmat, which then uses that information to verify each individual label during production. The printers, too, are given the parameters needed to print the correct “best before” dates or order-specific codes. All of that makes possible fast, seamless batch changeovers. “Multiple orders can be handled in succession, with very short changeover times,” says Timo Frankl. That in turn enables Erdinger Weissbräu to minimize and prevent errors, bottlenecks and downtimes.
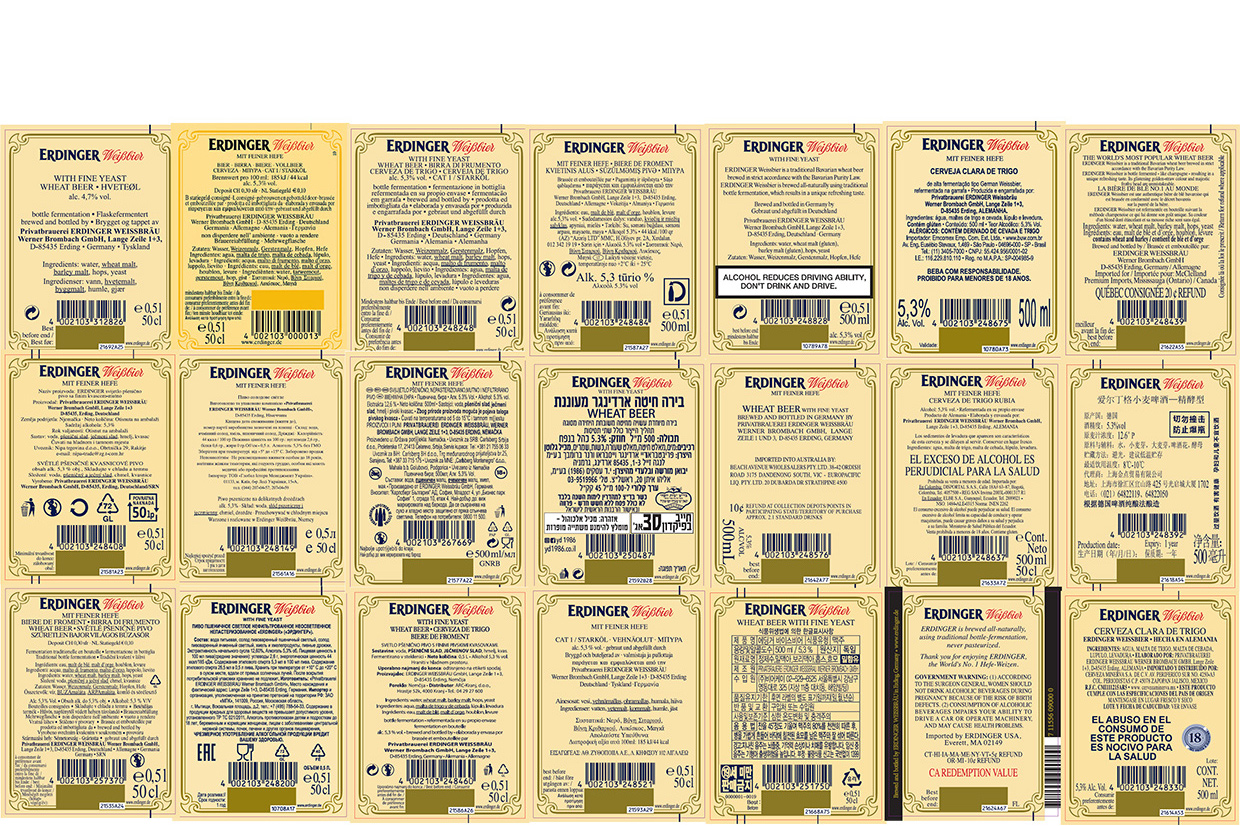
Erdinger Weissbräu
Line Diagnostics: Keeping an eye on everything, digitally
So, while Line Management takes care of controlling the filling processes, Line Diagnostics is all about monitoring and optimization. First, thanks to the digital solution, the lines’ performance can be viewed on monitors in the production hall at all times. Are all machines running? Are there any backups or stoppages? “The machine operators can also see at the end of the line what is happening at the start and can therefore quickly intervene if necessary,” explains Timo Frankl.
The machine operators can also see at the end of the line what is happening at the start and can therefore quickly intervene if necessary.
Timo FranklHead of Sales Global Digitalization and Digital Services at Krones
The production managers also have continuous access to information on machine status, allowing them to monitor and control the production processes. What caused a downtime – was it a planning error or a technical fault? How did this downtime impact other machines in the line? Automatic failure analyses can detect and troubleshoot potential errors or downtimes early.

Erdinger Weissbräu
In order to optimize overall equipment effectiveness (OEE), Line Diagnostics runs continuous analyses on the processes and examines the frequency and duration of downtimes and their most common causes. In addition, Line Diagnostics runs analyses on consumption – of materials such as bottles, labels and cartons but also of electricity and water. In short, Line Diagnostics delivers the information and analyses needed to initiate improvements and continuously optimize production processes.
Manufacturing Intelligence: Analyzing everything, digitally
Deeper analysis is provided by the Manufacturing Intelligence solution from Krones. It pulls data from Line Management and Line Diagnostics and uses it as the basis for generating order-specific reports. As a result, machine performance and material consumption can be compared across orders.
The three solutions at a glance
Line Management takes care of:
- Active control of the filling orders along the line
- Automatic setting of parameters on machines and other areas such as labeling
- Material validation by way of scanners
Line Diagnostics takes care of:
- Real-time visualization of the entire filling and packaging processes, with status information for each machine
- Automatic fault analysis
- Continuous analysis of various metrics and downtimes based on overall equipment effectiveness (OEE)
Manufacturing Intelligence takes care of:
- Self-service reporting for production
- Linking time-specific metrics (from Line Diagnostics) with orders (Line Management)
- Tracking and tracing across all systems along the value chain
Seamlessly integrated
In order for the digital solutions from Krones to do their jobs, they must of course be connected to the IT systems. That is especially true of the SAP system, which Erdinger Weissbräu only just implemented as part of this IT project. The modules used are ERP (Enterprise Resource Planning), EWM (Extended Warehouse Management) and LIMS (Laboratory Information Management System). The Krones solutions access important data such as material information, bill of materials and order details from the SAP system. At the same time, they deliver feedback on filling orders and on the movement of goods in order to ensure the smooth flow of information within the system environment.
Smart decision-making – today and tomorrow
Seven years in the making, SAP implementation, streamlining the system environment and implementing digital services – this IT project was no small order. Our partners at Erdinger Weissbräu are certain that these digital services have rendered the complexity of production and filling processes far easier to manage. Today and tomorrow. Because Krones offers its customers long-term support for its digital solutions. And that also means that Erdinger Weissbräu has made a sound investment for its future.