Procurement problems, sustainability-boosting initiatives and, not least, financial aspects. There are many reasons why beverage producers have stopped replacing defective assemblies with new ones and instead are commissioning Krones to have them professionally repaired or replaced with existing, fully reconditioned components. No matter which variant the customer chooses, both options support the responsible use of resources and actively turn the circular economy into everyday reality – a model that is about to become established practice as a genuine alternative to our current throw-away mentality.
Don’t throw it away, repair it! The replacement programme and overhaul service offered by Krones are viable alternatives to discarding assemblies in need of repair and to buying new spare parts, which can sometimes prove difficult, especially for components of relatively old machines.
Replacement
The replacement programme offered by Krones works as follows: First the assembly in question is removed from the line and an equivalent, fully reconditioned component from stocks is installed in its place. This plug-and-play method reduces machine downtimes and minimises production losses. Customers can pick a time for assembly replacement that fits in with their production operations, and ensures a high level of flexibility.
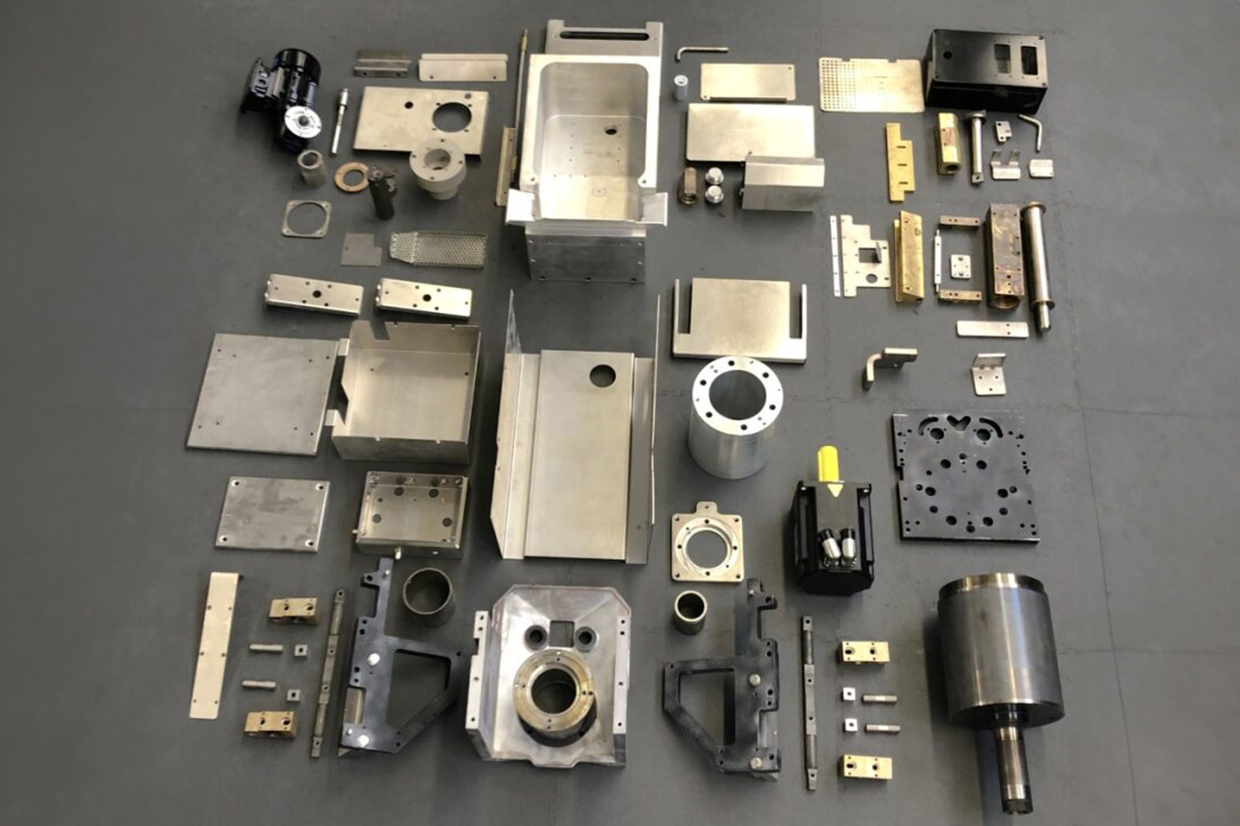
The component in need of overhaul is then sent to Krones where it is gutted, cleaned, measured and repaired. After it has passed a quality test, it can be stored in our warehouse as a fully reconditioned assembly. Following the closed-loop principle, it is now once again available for the next replacement job. “For standardised components in stock, the customer can always choose between having the defective assembly replaced by a fully functional and reconditioned one from our stocks or having it repaired and re-used on site,” explains Martin Sigl, Head of Module Assembly.
In-house overhaul
Depending on the degree of customisation, however, it may be advisable to have the assembly in question overhauled and re-installed in the machine from which it was removed. “Such heavily customised components will usually be completely reconditioned at Krones and then returned to the original machine,” emphasises Martin Sigl. The in-house overhaul option is mainly chosen for screw-capper assemblies and filling valves, for example. At present, between 10,000 and 12,000 of the latter are reconditioned each year by Krones and then re-installed in the original machine. “After we’ve received an assembly for repair, it usually takes three to five working days to completely recondition and clean it before returning it to the customer. The exact duration depends on the technology involved in each case,” says Martin Sigl.
The figures back up the success
Assemblies like lift cylinders, gluing or cutting units and centring heads for labellers, most of which are highly standardised, are obvious candidates for the replacement programme, which offers the advantage of shorter machine downtimes. “We currently receive orders for replacing about 4,000 to 4,500 centring heads per year,” says Martin Sigl. On the other hand, old or defective electronic assemblies, such as LCT3 controllers, or the camera and lighting systems of inspectors, are suitable for either of the two options. Whether such units are sent for an in-house overhaul or replaced by an equivalent substitute will depend on the specific conditions in each case.
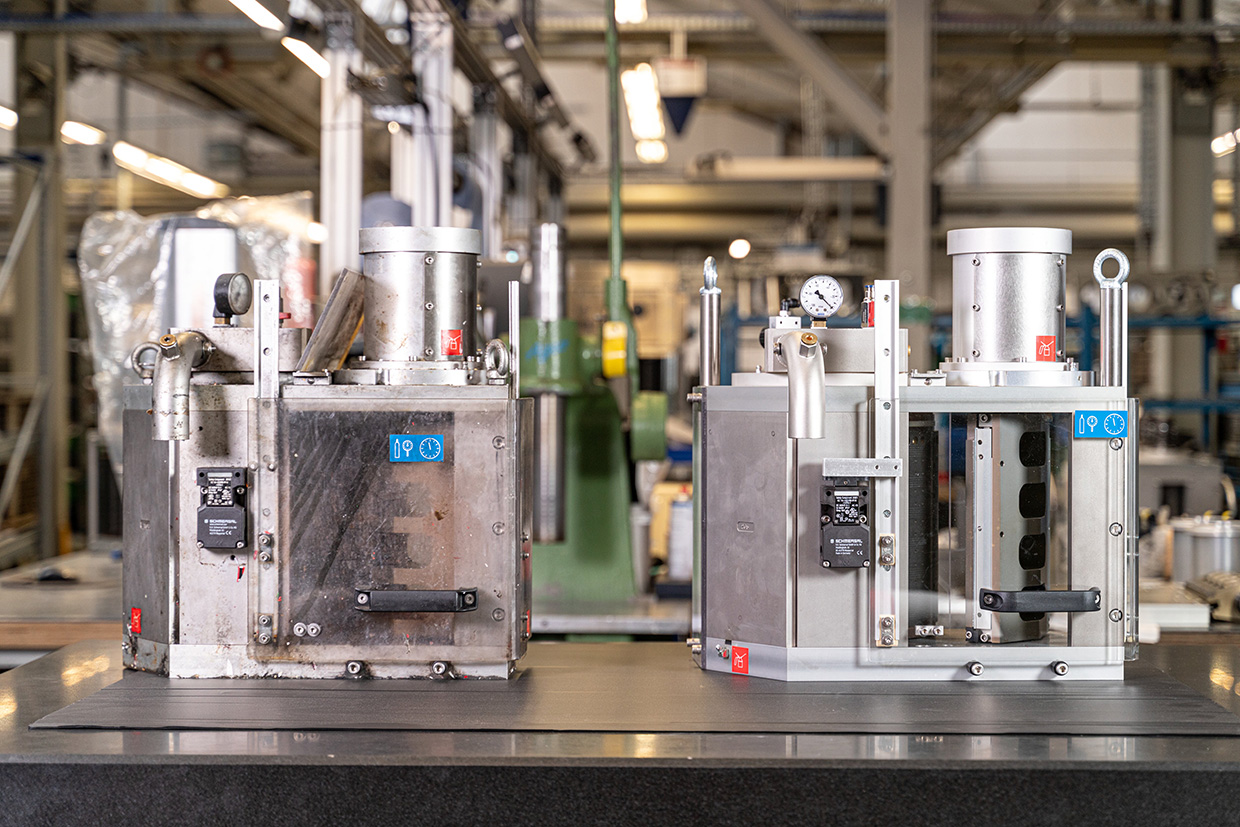
The “Turning old into new” options offered by Krones in the form of replacement or refurbishment have definitely proved persuasive, as demonstrated by the growth figures of the replacement programme. Demand for cutting units alone has tripled since 2018. “We’ve seen an annual rise of about ten per cent for filling valves, too,” says Jasmin Sturm. Within the Krones Lifecycle Service Inhouse and Repairs department, she and Victoria Schmidt are responsible for drawing up the quotations for replacement programmes and in-house overhauls, managing the relevant time schedules and coordinating the logistics involved. “It’s true, the number of enquiries we get varies depending on the type of assembly involved, but overall we’ve been observing a clear upward trajectory over the past few years. And for very good reason: If we perform a necessary overhaul here at Krones, that reduces the workload of the customer’s technicians,” explains Victoria Schmidt.
“What’s more, the prices we quote for overhauls and replacement units are usually substantially lower than the cost of an equivalent new component,” adds Jasmin Sturm. “Depending on the product in question, customers can save up to 50 per cent with a replacement. What is decisive for in-house overhauls is the general condition of the assemblies sent for reconditioning.” And since demand is steadily increasing, the aim is to scale up these options in the near future and include further assemblies in the in-house overhaul and replacement programmes. “So you see, we’re continually developing in this area, too,” affirms Victoria Schmidt.
The prices we quote for overhauls and replacement units are usually substantially lower than the cost of an equivalent new component. Depending on the product in question, customers can save up to 50 per cent.
Jasmin SturmSales coordinator in-house processing at Krones