Quite a few of these lines originate from Krones. Which is why experts from a number of our specialist departments have already looked into the EU directive at an early stage. I contacted two of them for an interview in MS Teams while working from home: Johannes Plankl, product manager for Filling and Capping Technology and Aurelie Börmann, who works as a chemical engineer in Packaging Design and Application.
Beverage packaging is about to undergo a visible change – at least in the EU. Why? Because in the future, the caps of non-returnable plastic bottles must be designed so that they remain connected to the bottle even after opening. To make the transition as smooth as possible, the industry is already getting ready for its introduction, even though the regulation does not come into effect until 2024. As the advisors from PricewaterhouseCoopers forecast in a study, around 1,350 bottling lines EU-wide will need to be prepared to handle tethered caps.
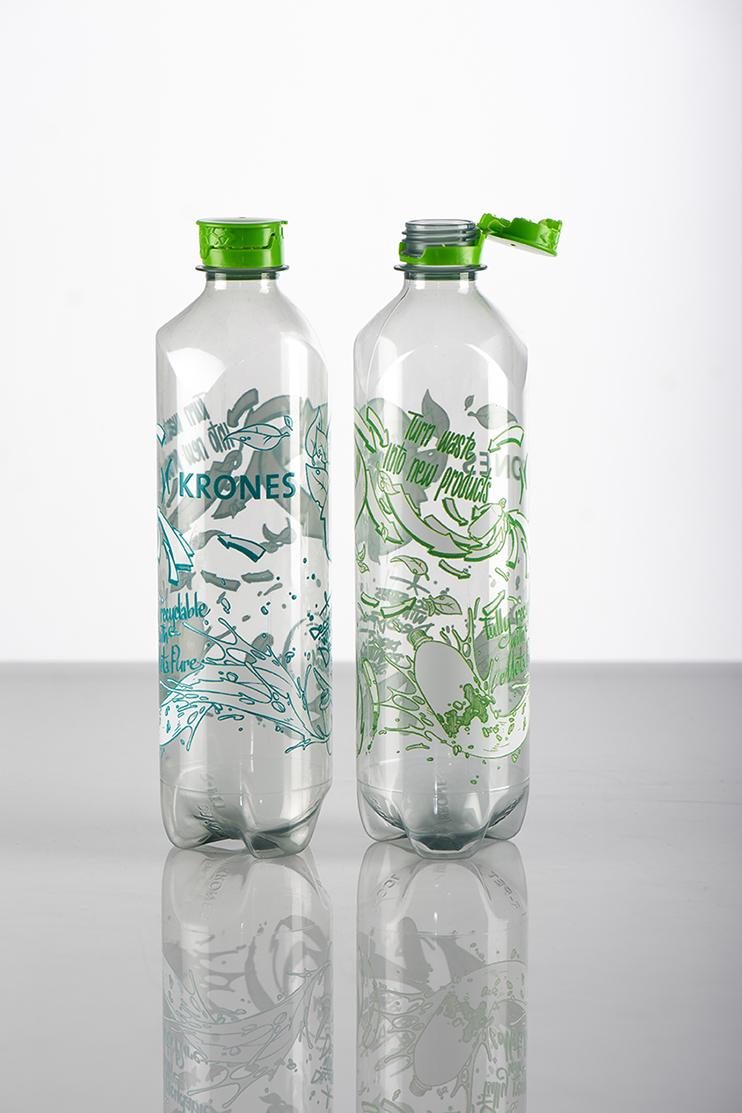
Aurelie and Johannes, how long have you been working with tethered caps?
Aurelie: When I started at Krones in 2017, the development of a bottle for tethered caps was one of the first projects that I contributed to. The EU directive was not published until two years later, but a similar legislative proposal had already been discussed back then in California. The cap manufacturer Aptar was looking for a partner to collaborate with on the development of a suitable tethered cap. The collaboration resulted in the FlipLid, which we presented together with Aptar for the first time in 2018
Johannes: Generally speaking, I must add that this subject is not entirely new to the industry. Even though there has been no legal obligation for it so far: cap systems that remain connected to the bottle have been on the market for quite a while – and are already being used by some beverage manufacturers, including Krones customers.
Tethered caps will be obligatory in the EU as of 2024. How is Krones preparing for this?
Aurelie: We in the plastics technology division for example, are participating in the formulation of a proposal about what form a sensible standard for tethered caps could take. Currently there is only a general specification stating that tethered caps must be used – and does not specify which exact basic conditions need to be met when doing so.
Why are you working on such a proposal and what exactly will happen with it?
Aurelie: The overall proposal is being drawn up as part of an EU work group: CEN, the European committee for standardisation, asked the industrial body CETIE, to present such a proposal. And because Krones is a member of CETIE, we are actively collaborating in this project. The definition of the standard is ultimately the job of the EU, but we can get involved with an advisory role. For example, the question of what minimum force the caps must withstand before they become detached from the container is discussed there. It is important here to find the correct balance. The greater the pull-off force, the more material is needed to manufacture the cap. And this basically contradicts the current efforts, which require that we strive to be as economical with materials as possible.
Do tethered caps also have implications for the bottle design? Or do they perhaps even stand in conflict with the use of lightweight containers?
Aurelie: No, tethered caps merely have an influence on the neck design, meaning the neck finish. Whatever happens above the support ledge is basically of no importance for the bottle.
Johannes: From a capping technology viewpoint, it is important that the neck finish can withstand the head pressure and that the diameter of the neck ring is large enough to stop the bottle from rotating in the capper. We also work closely with the various cap manufacturers to clarify such questions.
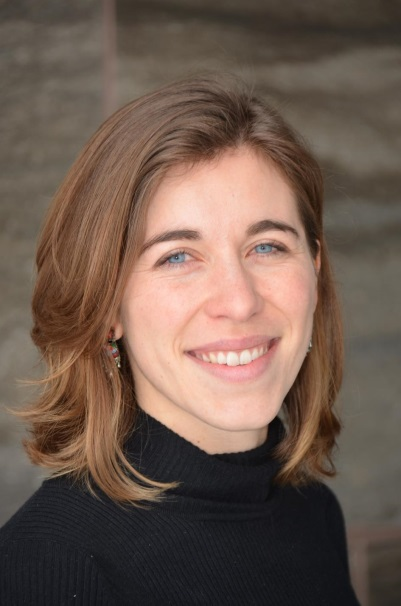
What form does this collaboration take?
Johannes: Cap producers provide us with samples of the different tethered caps beforehand. We then test them extensively in our technical centre to determine their suitability for processing and then inform the manufacturers of the results.
What factors must be taken into consideration for processing suitability?
Johannes: For example, with which force and movement the cap must be applied to the bottle. A differentiation can be made between two different types of tethered caps: firstly, screw caps and secondly so-called snap-on caps, which also include, for example, caps for cooking oil.
For screw caps, the combination of a twisting and a relatively gentle pushing motion is sufficient to apply them. Snap-on caps on the other hand must be, in a sense, hammered onto the neck finish and the pressure must be held for a period of time, as otherwise they will fall off again. The exterior contour of the caps also plays a major role as the selection of the capper heads also depends on it.
Can you explain this in a bit more detail?
Johannes: In the PET sector, we work with two different types of capper heads: cap retainers and grippers. The retainer slides over the cap from above, which means that it is only suitable for caps with a rotationally symmetric exterior contour. However, there are also caps which are equipped with a hinge for example, or have a projection on the side, which allows them to be flipped open with your finger. We use a gripper for them. It works in a similar way to a human hand, which can also grip objects with the most varied exterior contours.
What conclusions have you now drawn from the tests?
Johannes: Mostly that we can be reassured. We have found out that we already have a solution for every available tethered cap variant. With our current range of cappers, we can cover everything and this allows us to be relaxed as we look towards 2024.
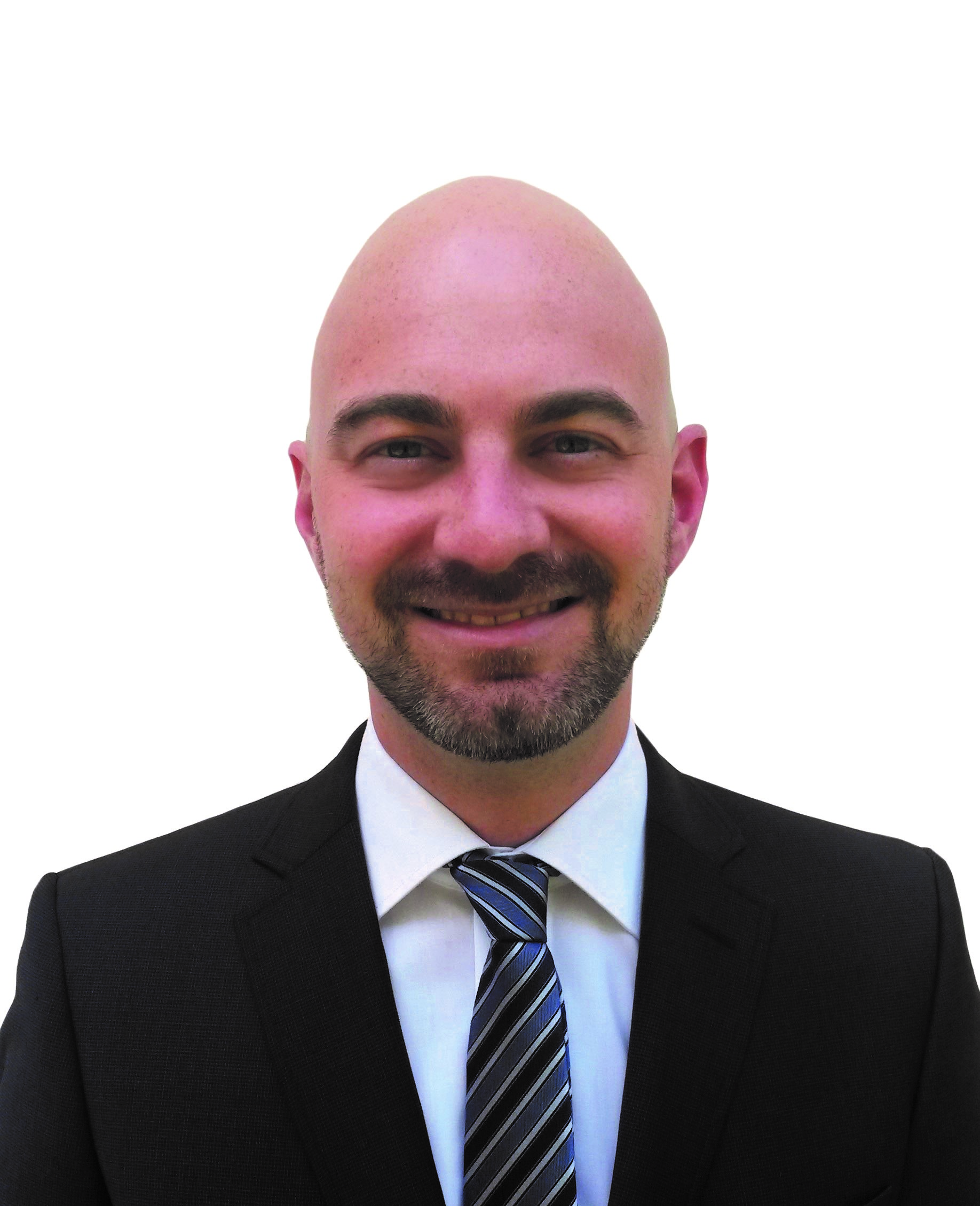
Most bottlers are sure to handle the tethered caps on existing lines. What conversion work can our customers expect?
Johannes: It all depends upon which type of tethered cap is used. Customers who decide in favour of a screw cap with a slit and keep their previous neck finish geometry will merely have to replace their cap retainers, as the exterior contour of a tethered screw cap only differs minimally from that of a conventional screw cap. In other cases, we need to check each individual cap type to see what parts of the machine technology need to be changed.
To finish off, I would be interested in hearing your opinion: What is your own personal view of the EU directive?
Aurelie: The EU directive addresses multiple topics referring to non-returnable plastic materials. For example, it sets out recycling quotas and prohibits certain non-returnable articles, which are currently landing in nature with particular frequency. This is why it most definitely makes sense. Alone if you consider that it has directed attention to the protection of the environment and resources – and not only here in Europe. But specifically when it comes to tethered caps, the question is not so easy to answer. The degree to which the actual benefits warrant the extra expenditure – especially the extra amount of material – remains to be seen.
Johannes: Yes, I have similar views. I personally would prefer it if we here in Europe were to simply set up a comprehensive bottle return and recycling system as soon as possible.
Aurelie and Johannes, many thanks to both of you for this informative discussion!
For everyone who wishes to find out more about tethered caps and the EU directive I have a literature recommendation:
Our plastics technology product specialist Jochen Forsthövel has summarised all of the most important facts about the subject in a whitepaper.