Filling carbonated and non-carbonated water into PET
Volumetric filler
- Electronic filling system with inductive flow meter or mass flow meter
- Pressing-on process without curves
- Infinitely adjustable flow speed
- End of filling after signal from flow meter
- Product feed from top via adjacent product tank
Field of applications
- Filling of both carbonated and non-carbonated water into PET containers, with and without conductivity
Output
- Up to 86,000 bottles per hour
VFS = Volumetric filling system, Flow meter, Short tube
Functional principle of the valve
The filling valve moves electropneumatically onto the PET container without a stroke control cam. Afterwards, the container is pressurised. Once the same pressure is in the product tank and the PET container, the filling valve will be opened and the filling process starts. The liquid is gently fed via a swirl insert into the bottle. With the PFR valve, the speeds are infinitely adjustable, guaranteeing optimum flow behaviour. A flow meter monitors the fed liquid quantity. Once the exact filling volume has been reached, the flow meter provides a signal and the valve closes electropneumatically. After a settling phase, the pressure in the head space of the PET container is reduced via a snifting valve and the filled product exits the machine.
Conductivity: > 20 μS/cm
Viscosity: < 10 mPa·s
Pulp: ≤ 0.4 mm/proportionally < 10 %
Fibres: 1 x 5 mm/proportionally < 5 %
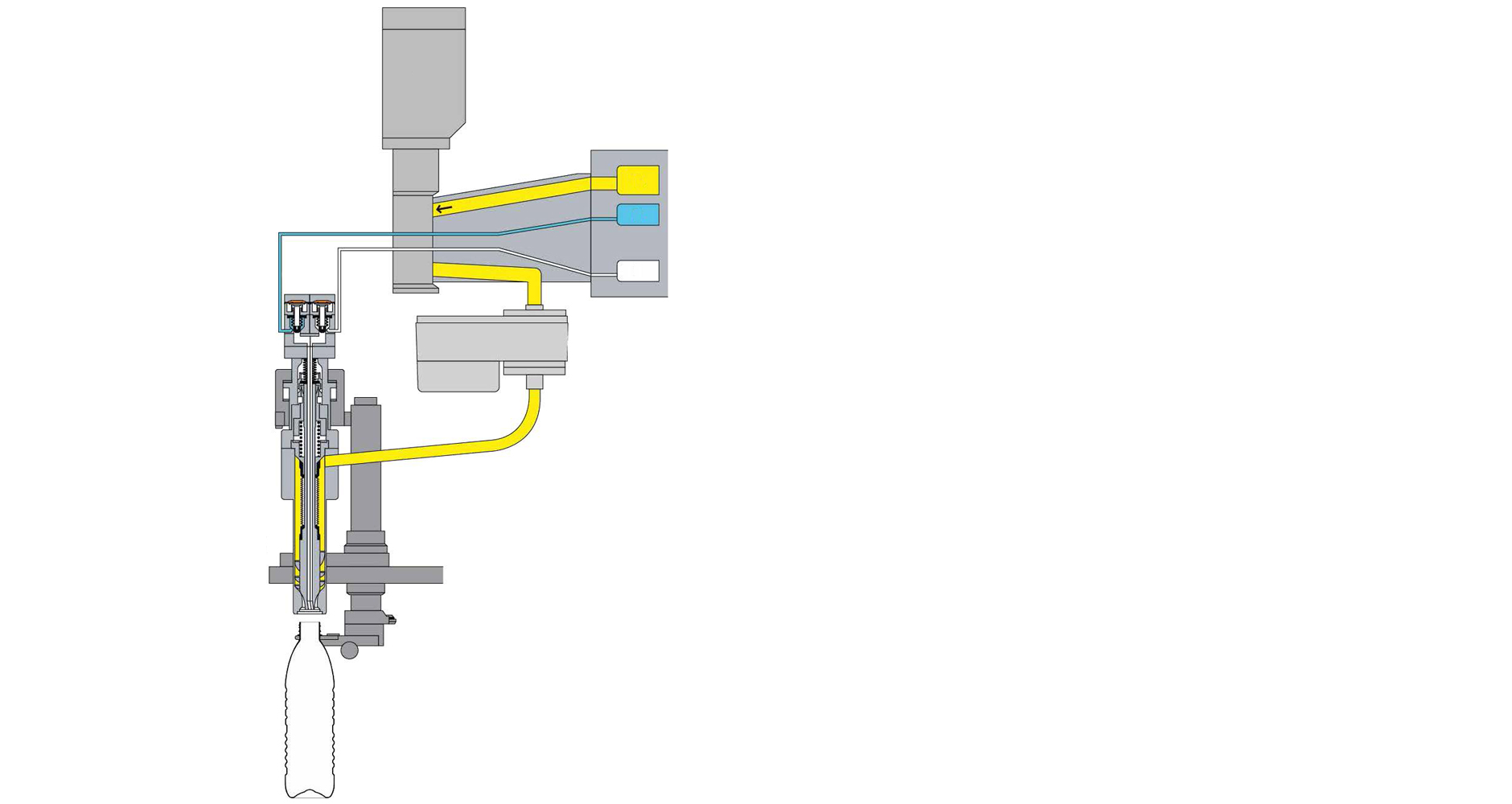
Variants
Modulfill VFS with PFR valves plus Krones Contiflow | Modulfill VFS-M – integrated filler-mixer block |
---|---|
![]() |
![]() |
The Modulfill VFS with PFR valves can be optimally combined with the Contiflow mixer. In addition to the advantages of the PFR valve, beverage producers benefit from the optimised communication between the two machines. | With the Modulfill VFS-M, the "M" stands for "Mixer" – which is directly connected to the filler. The product is directly fed via the raised carbonation tank into the manifold. The conventional filler bowl is no longer required. Thanks to optimised interfaces, the number of components is also reduced - and thus not only the footprint is reduced, but also the running operating costs. |
Benefits to you
Maximised flexibility
Non-carbonated and carbonated products can be filled on one system.
Enhanced product quality
The new PFR valve enables optimum adjustment of the filling speed to suit the particular product properties. Products which tend to foam excessively can also be processed.
Increased output
The filler operates without lifting cam, which increases the filling angle: This in turn increases the output, and that for the same line size. Filling water with a PFR valve, for instance, will increase the annual output by up to 25 per cent, that is 72 million bottles (based on 0.5 litre bottles and a pitch diameter of 4,320 mm).
Reduced product loss
Thanks to the adjacent product tank, the product can be fed to the filler from above, reducing product loss to a minimum (optional: Modulfill VFS-M with integrated mixer and raised carbonation tank).
Improved cleaning
The CIP cups automatically swing into place using a magnet. This contact-free process without pneumatic components optimises the hygienic conditions and enables the installation of more filling valves on a pitch diameter.
Saved energy and raw materials
The PFR valve operates electronically. This saves 30 percent of compressed air when compared to electropneumatic filling.