Microbiologically-safe process for cap disinfection with H₂O₂
For safe cap disinfection
He who counts on a very safe microbiological process for the disinfection of containers and caps should go with gaseous hydrogen peroxide as the ideal sterilising media. The gaseous medium is distinguished by its short treatment times and at the same time it reaches every single angle of the surface to be disinfected. This is exactly why it is predestined for cap treatment. Krones has further developed the CapAsept D disinfection system and specifically optimised the sterilisation distance for caps.
At a glance
- Safe sterilisation of sports caps and flat caps
- Output: up to 72,000 caps/hour
- Further development: single-track treatment spiral instead of the long and in parts double chute tracks
- Result: low consumption of H2O2 and energy
- Reduced space requirement: low building heights are possible*
* Compared to conventional sterilisation units
Method of operation
First the caps enter the sterilisation unit via an infeed chute. A stepper motor ensures that the caps have a certain distance to each other. Then the caps slide onto the turning rotor unit or better onto its perforated plate. The rotation movement gently pushes the caps along the single-lane treatment spiral from the inside to the outside.
The advantages
- The caps can be effectively treated with gaseous H2O2 from all sides.
- There is no friction between the caps or between the caps and the unit.
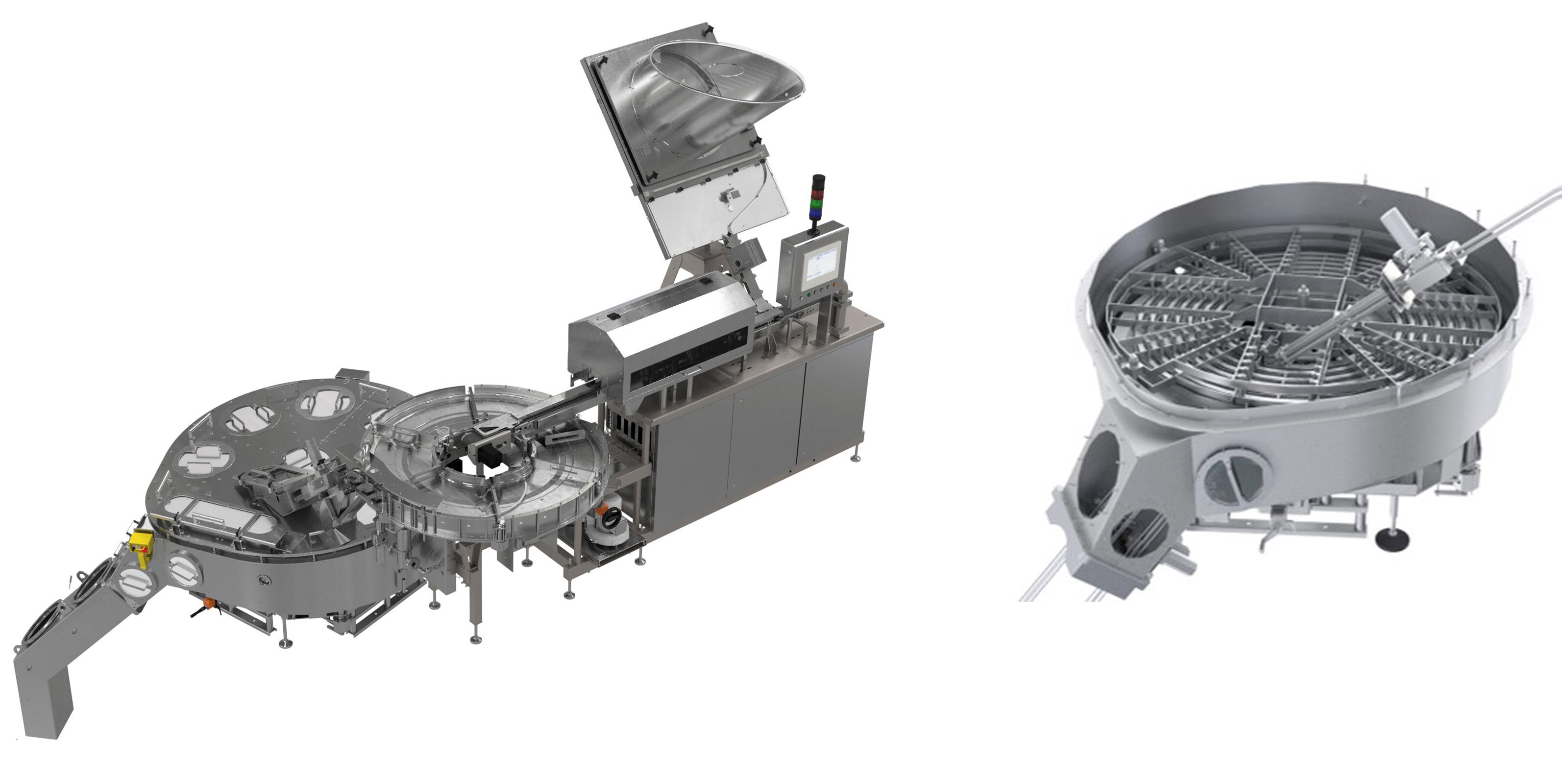
Flexibility for several cap variants
Infeed and discharge chutes
- Designed for the respective cap sizes
- Adjustment with special ready-to-use change parts
Treatment spiral
- Uniform design for a large range of caps (e. g. 28 to 38 mm)
- No use of change parts required
Floor-guidance spiral
- Variably adjustable height adjustment of the guidance height: secure guidance of different cap heights
- Adjustment via a crank outside the unit
Hygienic treatment room
Low installation height
The redesigned version of the sterilisation unit is distinguished by its new and flat design. This way, it can be easily incorporated in production areas with low hall heights.
Combination with Krones cap feed systems
- Uniform interfaces: trouble-free connection of all aseptic feed systems (sorter or sorting elevator)
- Flexibility: Combination of up to three sorting elevators as well as small or large cap buffer system possible
- Process safety: inclusion of the inspection units
Benefits to you
Increased operator comfort
The low construction height also improves the accessibility to all essential areas and the infeed and discharge chutes can be easily replaced in just a few steps.
Safe cap conveyance
The infeed chute as well as the treatment spiral are in single-track design. This allows for the caps to run through the disinfection unit without accumulating or pushing each other.
Combination with Krones cap feed systems
With its new flat design, the CapAsept D can be ideally combined with Krones cap feed systems. This way, both units can be installed also at very low hall conditions.
High performance at flexible treatment times
The gaseous hydrogen peroxide disinfects the caps safely with a short treatment time (approx. 12 to 18 seconds depending on the cap type).
Infinitely variable height adjustment of the guidance height possible
CapAsept D gives you the opportunity to flexibly select the cap type. This is because the guidance height of the floor-guidance spiral can be infinitely adjusted to suit the respective cap size enabling you to process many different cap types without any time-consuming change-over work.