The all-rounder in the latest generation of high-performance blow moulders
The multi-talented moulder for different process types
Its variance remains the absolute benchmark. All process types in one line! It also outperforms everything that came before it in terms of energy consumption. The new generation of the Contiform Heatset is here! It uses the market-proven technology of its predecessor - but only as a basis. For be it flexibility, hygiene, user-friendliness or digitalisation: In the course of a complex development project, the blow moulder has been given a whole series of new features and optimisations.
At a glance
* Dependent on the processing range and design of the machine
The newest generation of Contiform
Design
The Contiform Heatset has a modular design and can be individually equipped to meet all requirements.
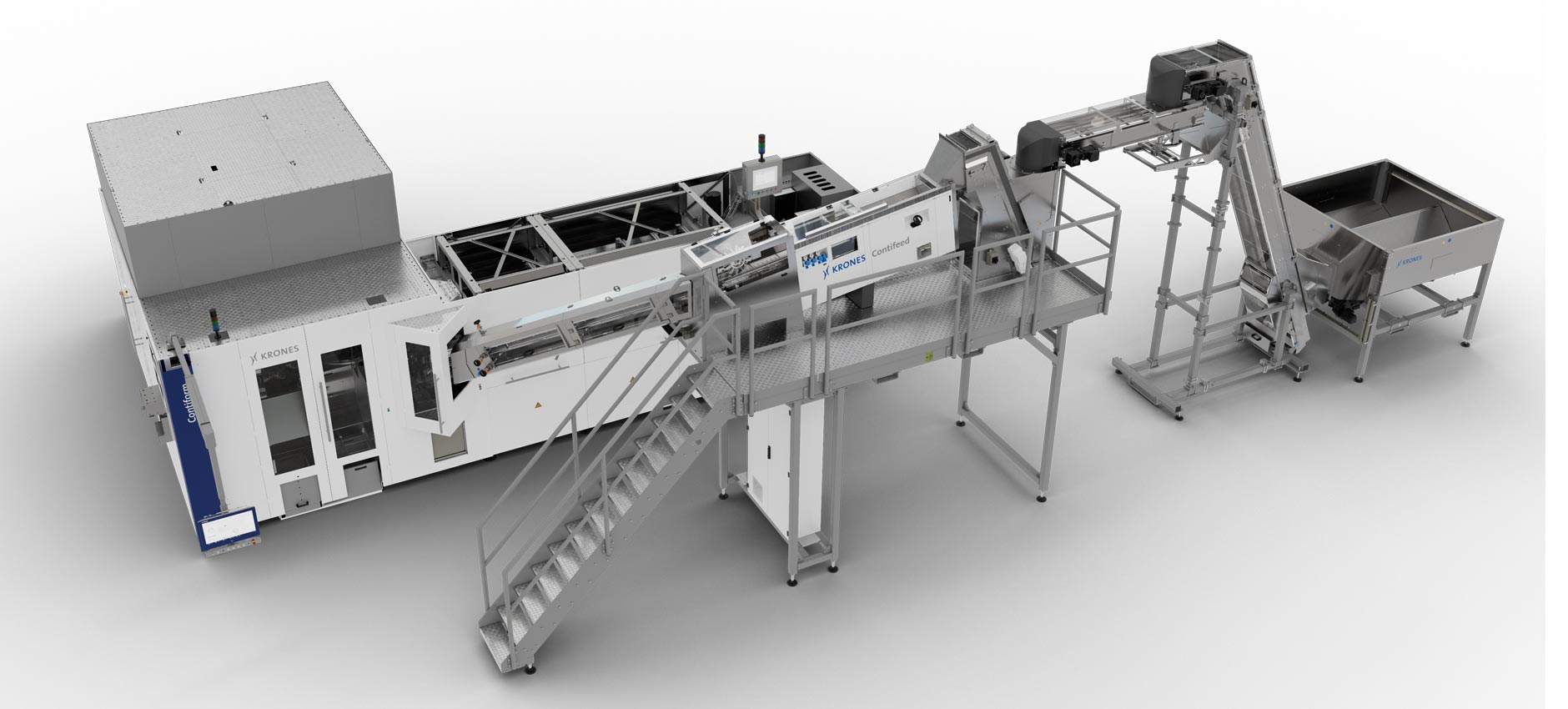
Basic machine
- Linear infrared heating module for processing preforms with a length of up to 160 mm and a support ledge diameter of up to 48,5 mm
- Blowing module with blowing stations for manufacturing containers of up to 3.5 litres
Components
The Contifeed preform feed system
Focussed on performance right from the beginning
At a glance
- Applicable with lightweight, standard and heavy preforms
- Three models – suitable for the respective blow moulder output
- Two variants of the feed rail:
- Gravity system for all common preform types
- Air-assisted – ideal for lightweight preforms and high-speed applications
- Optional:
- Automatic adjustment for quick change-over
- Hygienic design
- Soft-tilting preform tipper for a particularly gentle preform infeed
Benefits to you
- Automatic troubleshooting
- Quick and infinitely variable adjustment to every preform type
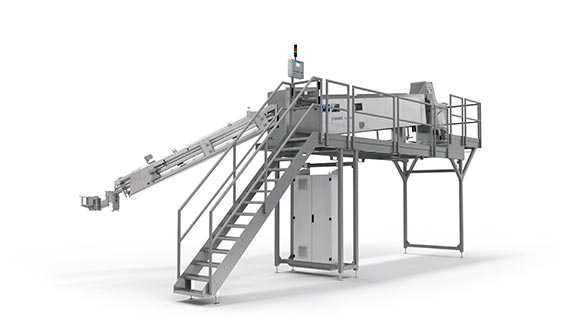
Contifeed with automatic adjustment
Infrared heating technology
Efficient and flexible
Heating tunnel
- Very small oven chain (36.4 mm or 50 mm)
- Additional reduction of the heating room
- Adjustable base reflectors: adjustable to the respective preform length
- Maintenance-free system of ceramic reflectors
Heaters
- Parabolic reflector for the top infrared emitter
- Longer infrared emitters and smaller dead spaces between the heaters
Benefits to you
- Up to 15 percent smaller footprint thanks to reduced deadspaces
- Improved lightweighting potential through targeted heating of the preforms directly below the support ledge
- Up to 5 percent lower heating energy consumption due to shorter distances and parabolic emitter technology
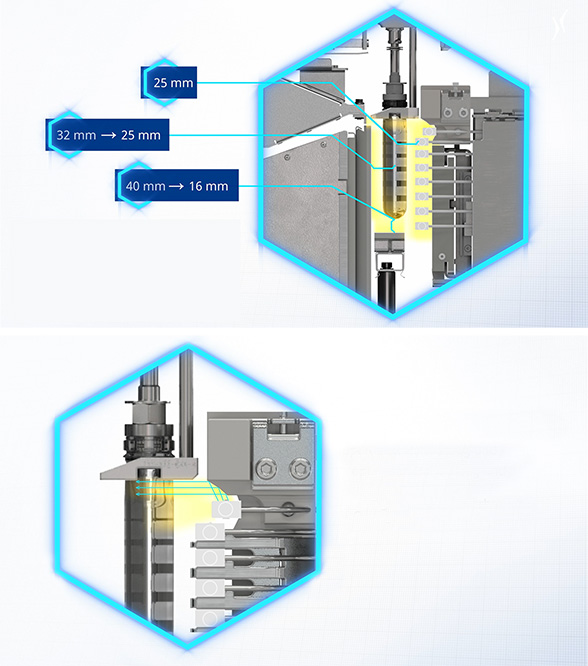
The Contiform blowing module
Robust and precise
Transfer system
- Five-point heating mandrel in the linear oven
- Only four internal horizontal preform and container transfer points
- Actively controlled transfer grippers
Platform and drive technology
- Torsion-resistant platform construction with skip-and-run technology
- Five high-precision Monotec servo motors with real-time synchronisation
Benefits to you
- Precise transfer of preforms and bottles
- Perfectly suited for very light preforms
- No PET dust deposit
- No change of handling parts if the neck finish remains the same
- Significantly reduced scrap rate thanks to skip-and-run technology
- Simultaneous change-over of heating module and blowing module possible
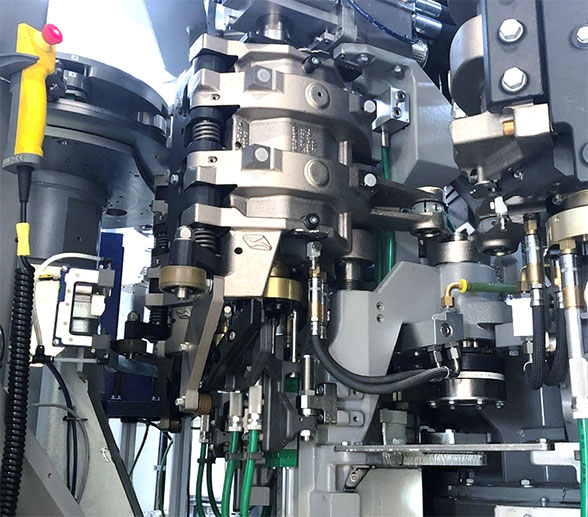
The blowing stations
Intelligent while saving on compressed air
Blowing stations
- Electromagnetic stretching system without air consumption
- Extremely low dead space volume in the entire blowing station
Compressed-air recycling
- Further developed, two-stage Air Wizard Plus compressed-air recycling system for the internal reuse of the compressed air
Benefits to you
- More flexible use of the process time through optimised compressed-air recovery
- Considerably lower valve switching time dispersion
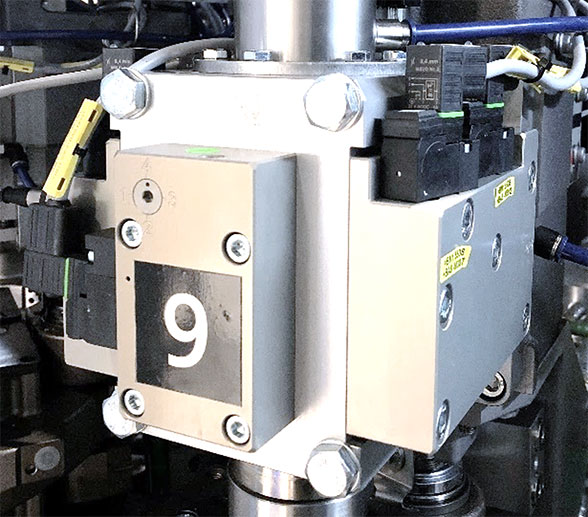
Better in combination: Contiform Heatset block solutions
A high output in a small space
Blow moulder and filler are an effective team. And that is the reason why we have perfected the popular combination of both machines even further in a single block. With a seamless drive concept, finely tuned transfer interfaces for every production program and precisely operating processes in stop situations, you can count on getting the very best out of your PET bottle line.
Contiform Bloc BF
- Blow moulder with filler
- Functions: Stretch blow moulding, filling and capping
Flexible block solutions
- More than 50 years of experience in block technology
- More than 2,000 Contiform block solutions sold worldwide
- More than 80 percent of all Contiform blow moulders are supplied in block configurations.
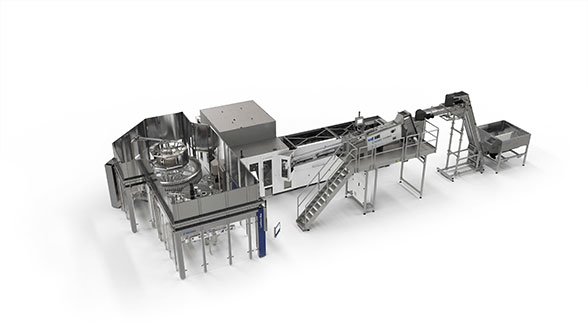
Bottle design and moulds
Creative and in line with the market
At a glance
- Four production centres worldwide with state-of-the-art manufacturing technology
- Container design experts at all four locations
- Design and production of mould types for all Contiform series
- Mould validation on our own technical centre systems
Benefits to you
- Customer-oriented consulting: Creative, functional, unique
- Individual designs with a view to customer requirements and feasibility in the beverage line
- Experience from more than 20,000 moulds per year
Benefits to you
Reduced heating energy consumption
Save even more: Further optimisation of the infrared heating technology reduces the energy consumption used for heating the preforms by an additional five percent.
Production efficiency
With its sturdy design and new functions, such as skip-and-run, the new Contiform Heatset continues to operate with the utmost reliability and with even less interference than before.
Maximised product range
No blow moulder produces a greater container variety than our Contiform H. From containers for non-carbonated and carbonated beverages through to hot-filled bottles: all of this is possible in one machine.
Ergonomic design and user-friendliness
The servo drives in conjunction with the improved rotary joint continue to keep the noise level stress-free, even at the highest output rates. The new operating interface with large touch-screen allows for even more efficient working with the machine.