New line and energy concepts thanks to revolutionary filling and capping technology
Think differently – and revolutionize the beer filling process
Revolutionary filling technology as part of a resource-saving brewery of the future. Released cooling energy that can be used intelligently in another area. A reduced microbiological risk during filling. Last but not least: Filling and capping in a single unit, in less than five seconds, and this at ambient temperatures. When it comes to the Dynafill, the list of true unique selling points is long –and it soon becomes clear: This machine makes it possible to achieve completely new energy and line concepts.
At a glance
- Combined filling and capping process on one single machine
- Maximum speed: 80,000 containers per hour
- The Dynafill enables the following:
- Filling temperatures of up to 30 °C
- Reduced energy requirement in the entire line
- Innovative line concepts
Filling and capping head
Filling and capping in one functional unit: what started out approximately ten years ago as a vision became reality in 2017 with the presentation of the first ever machine at the drinktec. Krones has since taken the Dynafillto series maturity, tested it in the field under the most diverse conditions and then further developed it based on the valuable feedback of experienced bottling companies.
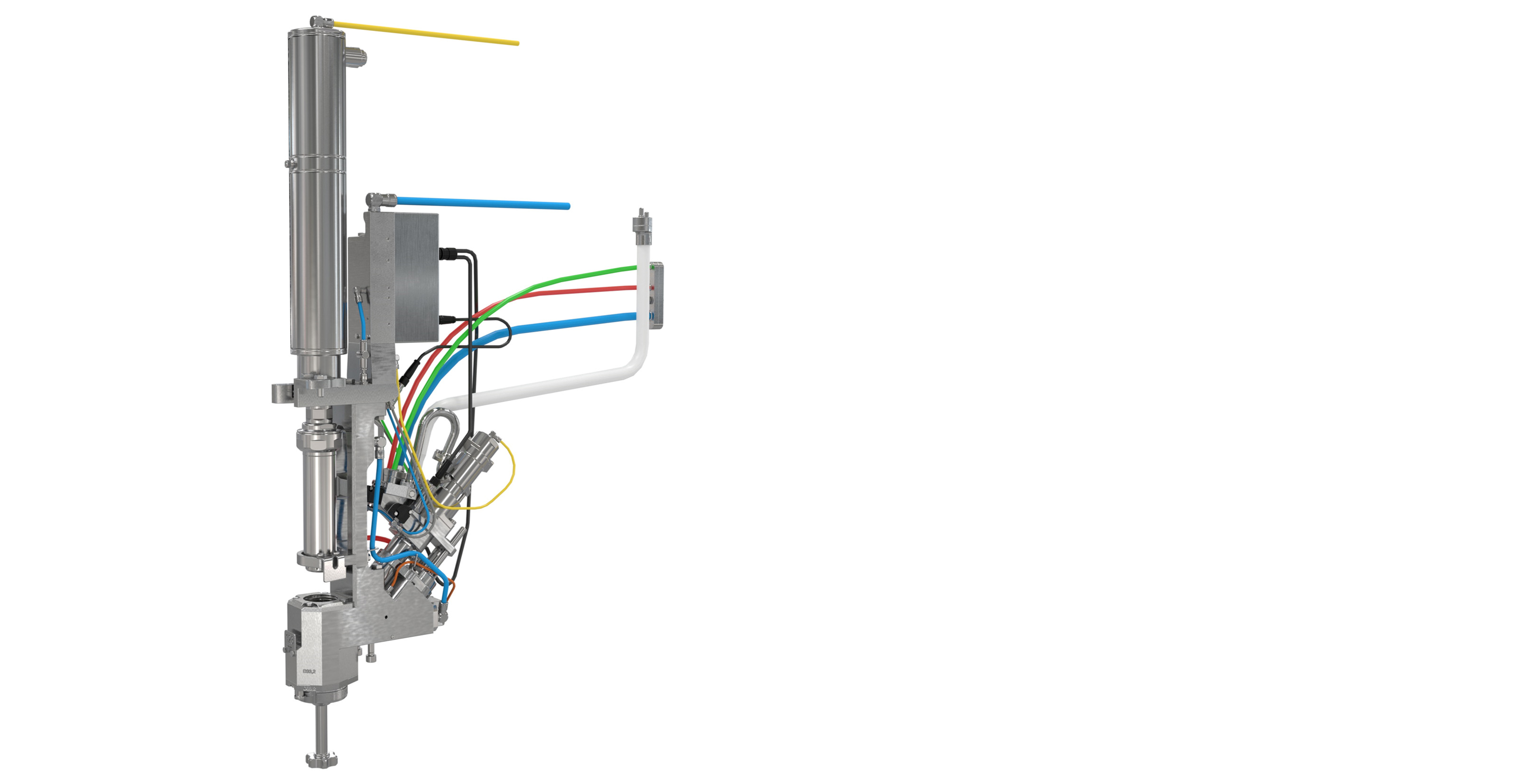
Also: dismantling device for user-friendly maintenance
Manually inserted CIP cup
Bottle neck seal for handing a variety of formats
Decentrally arranged pilot valves
Servo capper for standard and twist-off crowns
Filling valve that can be moved in a diagonal direction
Speed and footprint
Compared to conventional systems, the Dynafill reduces
- the time needed for the filling and capping process by 50 percent to around five seconds.
- the duration of the filling process to approximately just 0.5 seconds.
- the number of filling valves from 100 to 66, and this at the same speed of 36,000 containers per hour.
- the footprint by 50 percent, as neither a separate capper nor the corresponding transfer starwheelsare needed.
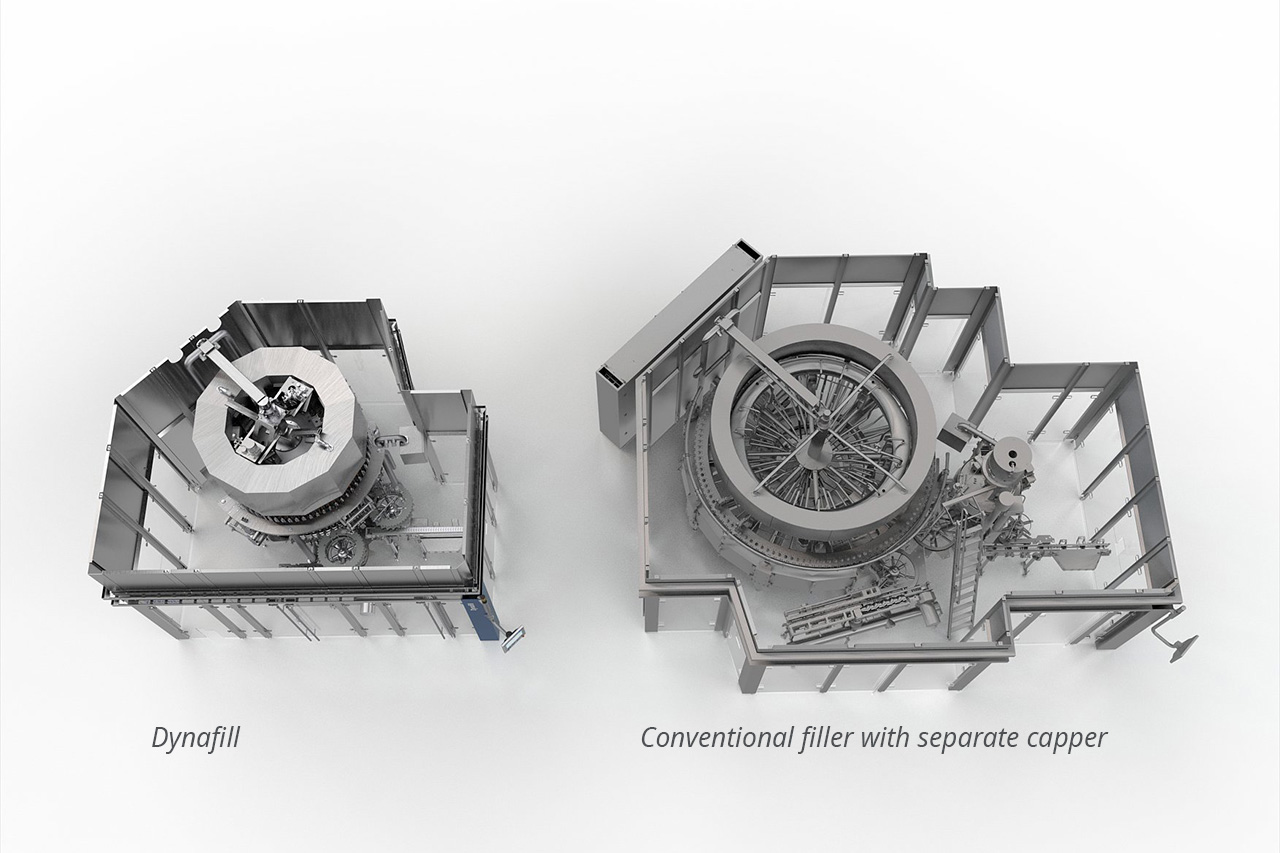
Innovative line concepts conceivable
The Dynafill not only has a positive impact on the filling quality, and thus the product quality, but also makes it possible to approach a line design from an entirely new angle:
- Due to the fact that the bottles are already capped on the Dynafill, even when the machine is at a standstill, no emptying section is required on the conveyors after the filler (as is the case in conventional filling systems).
- Thanks to a significantly lower footprint, it is now possible to reach output increases that would have been unthinkable thus far with a limited space requirement, even in Brownfield projects.
- Completely new design opportunities arise for Greenfield projects: On the one hand, the filling output remains relatively similar even if the container sizes differ (e.g. large container to 0.5 litre bottle) and, on the other, the machine footprint is considerably smaller. As a result, completely new line and conveyor routes can already be designed in the planning phase.
For a quick change: MultiGuide Base clamping starwheels
As in all of its fillers for glass bottles, in the Dynafill, Krones will also be using its MultiGuide Base multifunctional clamping starwheels for bottle handling in the future. Unlike the handling parts used so far, which are designed for just one container format and size, the clamping starwheels can handle the entire range with all conventional bottle formats.
Advantages:
- Change-over times are reduced to a minimum
- Lower amount of space required as the handling parts sets needed thus far can be omitted
- No risk of contamination as operator intervention is no longer required in the filling and capping area
- Should a gripper need replacing: Extremely simple and reproducible assembly in just one minute; no fine adjustment necessary
Benefits to you
Decentralised electronics
To decentralise the power supply to the electronics, the control block is now integrated directly in the filling valve. A smaller electronics cabinet can therefore be used.
Ideal cleaning conditions
The Dynafill is a closed system. The filling valve and the capper unit are integrated in the CIP circuit.
Reduced space requirement
Thanks to the 2-in-1 principle, the Dynafill requires substantially less space than comparable combined filler-capper units. As the filler is not to be emptied in the case of a malfunction in the filling line, the buffer section to the labeller can be reduced. The labeller can also be directly block-connected to the filler.
Increased outputs
In future, the Dynafill enables a higher total line output than conventional systems: A total of 80,000 containers per hour can be processed.
Stable filling process
The Dynafill enables not only cold but also warm filling of beverages (temperatures up to 30 °C) – the process does not take longer than five seconds in both cases. The filling process remains always stable.
Reduced CO2 consumption
The CO2 consumption is 20 percent lower than that of conventional systems.
Increased filling quality
The closed hygienic filling and capping area ensures optimum product purity, as return gas feed back into the product bowl is no longer required. High-pressure injection is no longer required and no product is lost during filling.