Krones wins 2017 Energy Efficiency Award
The energy-self-sufficient brewery proves persuasive for the expert jury and the general public
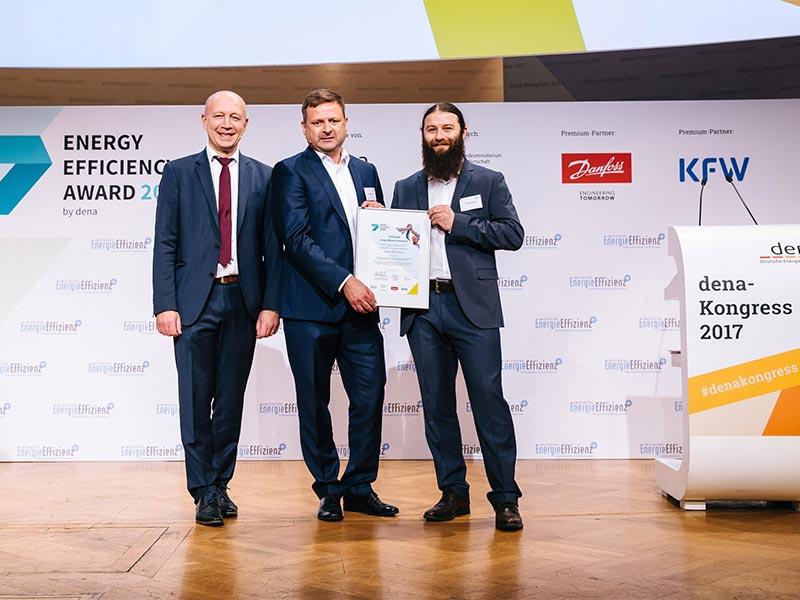
CO2-neutral beer? This may at first sound like a utopian flight of inebriated fantasy. But Krones AG is deadly serious. Because the technology conglomerate from the Upper Palatinate has crafted a plan that’s as detailed as it is future-friendly, designed to get a genuinely energy-self-sufficient, CO2-neutral brewery up and running.
Krones’ development team has been progressing the “Brewery of the Future” research project for quite a few months. In September of this year, the concept had finally matured sufficiently to be showcased for the first time to a broadly based and above all keenly interested public at the drinktec, the sector’s premier trade fair.
The issue of energy-efficient brewing is a highly topical one not only for the trade public, but also for consumers, as evidenced last Monday, the 20 November, at the Congress of the German Energy Agency (abbreviated to: dena): following a persuasive pitch from Krones’ Product Manager Dr. Ralph Schneid, the “Brewery of the Future” won the Public Prize of the Energy Efficiency Award. The short list comprised three finalists, chosen by an expert jury in the run-up to the competition. The eventual winner was then determined by live voting during the afternoon at the prize-giving ceremony, after which the award was presented immediately.
60 per cent energy savings for brewery operators
Practical implementation of the energy-self-sufficient brewery features several meticulously harmonised technologies. Its key components include:
- a biogas system for recovering the residual substances
- a modified unit-type cogeneration plant for producing heat and electricity
- continuous seven-days-a-week production for smoothing out load peaks
- the EquiTherm energy recovery system, which feeds surplus energy from the brewhouse to other steps in the process
- a newly developed filling technology that enables the cooling energy available to be used for secondary processes.
For a beer production volume of 2.6 million hectolitres, the energy-efficient brewery generates an annual surplus totalling 1,534 MWh of heat and 1,066 MWh of electricity, which can be sold on to other customers. The savings in terms of electricity come to 30 per cent in comparison to a standard brewery, and for thermal energy even to around 60 per cent.
Download
