A quick beer
Beck's, Corona, and Budweiser are enjoyed around the world. They all come from Anheuser-Busch InBev, the world’s biggest brewing group, which produces around one-third of the world’s beer. The group’s portfolio encompasses 630 brands, made in 260 breweries. The Belgian conglomerate employs more than 170,000 people in over 150 countries – including South Africa.
AB InBev operates seven breweries here, including the Pretoria South African Breweries (SAB) site with almost 900 employees. This plant mainly produces the South African beer brand Castle Lite and the Mexican beer Corona, together adding up to some 8.5 million hectoliters each year. To boost production of Corona especially, the company has added a non-returnable glass line from Krones. “We chose Krones because of the good relationship, compatibility with current equipment and reliability standards”, says packaging manager Theo Govender.
Two times 50,000 bottles per hour on a single line
What makes this line special is its high speed, filling 100,000 glass bottles per hour. It’s actually two lines running in parallel, each with a capacity of 50,000 bottles per hour. And it makes this line one of the fastest in South Africa. This design offers AB InBev not only a high output but also the flexibility to handle different beers in parallel – for example Corona and Castle Lite at the same time.
“To fit perfectly in SABs hall concept this line is extremely compact, with shared operating areas. This allows operators to attend to multiple machines, thereby reducing the number of operators required,” explains Boris Tremmel, Head of Key Account Sales at Krones.
Flexible filling, labelling, and packaging
The Ergomodul modular labeler features interchangeable labelling stations, making it possible to switch over to the beer currently in production. Since Corona bottles feature applied ceramic labels, the labeler doesn’t come into play here. Corona bottles simply bypass it.
When it comes to packaging, SAB also has choices as the line runs two different packers: the Variopac Pro WT for wrap-around cartons and trays and the Variopac Pro PFS for shrink packs. Both are tried and trusted packers for non-returnable containers. The Variopac Pro offers easy change-overs and expansion, so changes to packaging concepts can be accommodated at any time.
Another unique feature is the use of the multi-functional clamping starwheel MultiGuide Base, a first for AB InBev. Since the top and bottom clamps can be opened independently of each other, it is able to securely grip bottles with widely varying diameters. The big advantage is that it does away with the need for manual intervention during format change-overs.
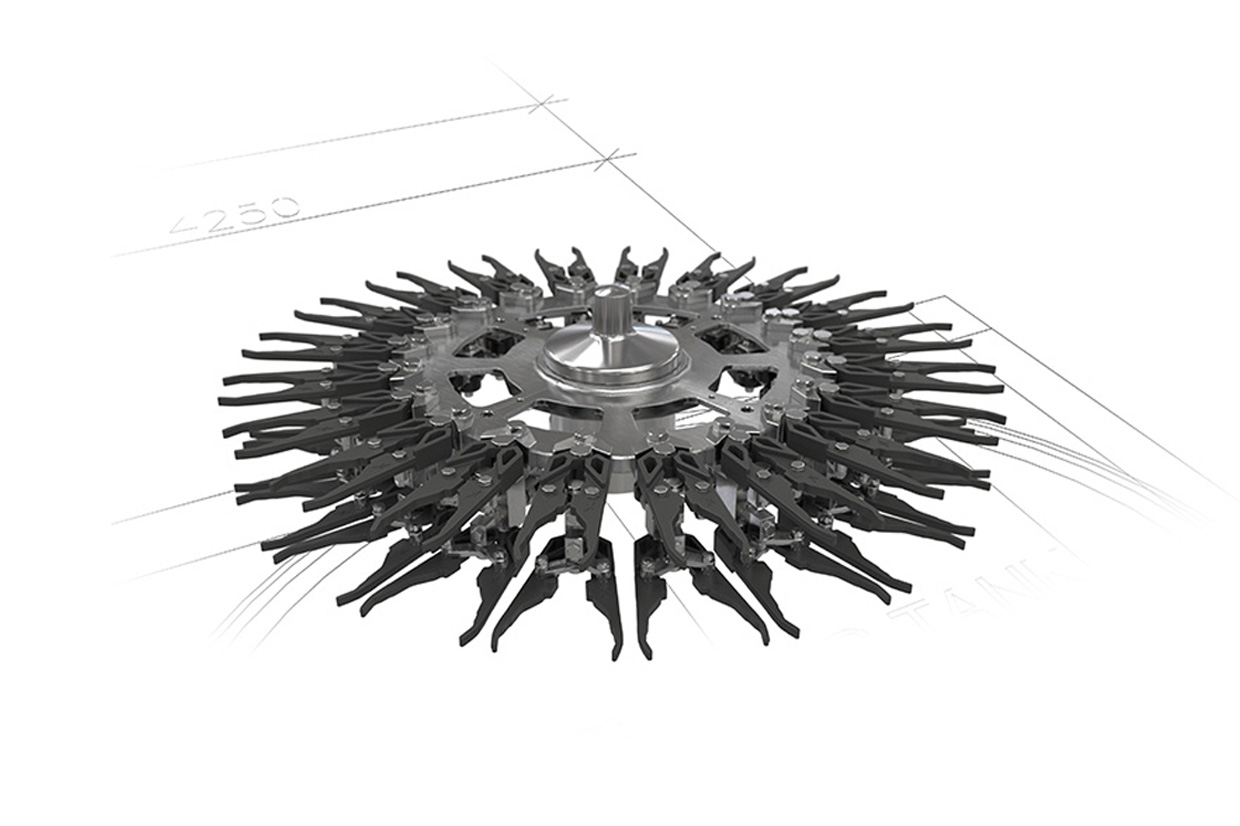
Download
