Recycling of PET containers into flakes or pellets
Sustainability and profitability: our contribution to a circular economy
Can plastic packaging be sustainable? Yes, if its production is gentle on resources and it can be kept in a closed loop – and Krones makes both possible. From a material-saving packaging design through to low-energy container production and the recycling of used plastic materials: We give PET bottles and other packaging the chance to have a sustainable and environmentally friendly life – not only once, but multiple times.
Recycling plays a key role here. On the one hand, Krones provides its own washing and decontamination modules and, on the other, also takes on the overall responsibility for entire recycling factories.
At a glance
- Recycling of PET containers into flakes or pellets
- Energy-saving, direct further processing (optional)
- Individually adjustable intrinsic viscosity (IV)
- Production of different material qualities –up to food-grade PET standard according to FDA, EFSA and other certificates
- Available as a complete line or in the form of individual machines
Three system types for PET recycling
MetaPure (complete system) | MetaPure W-PET | MetaPure S |
---|---|---|
Applications | ||
Recycling of containers supplied in bales/as pressed containers
|
Recycling of containers to form PET flakes for use in non-food products or for further processing for direct contact with foodstuffs | Decontamination and SSP** of washed PET flakes, or PET flakes or pellets for use in direct contact with foodstuffs |
Output | ||
1,000 kg/h to 6,000 kg/h | 1,000 kg/h to 6,000 kg/h* | 500 kg/h to 1,500kg/h* |
Space requirement | ||
600 –4,500 m2 | 250 –1,000 m2 | 250 –500 m2 |
* Several modules can be combined with each other in order to achieve higher outputs.
** SSP –Solid State Polymerisation
Who can use MetaPure?
- Brand bottlers
- Private label bottlers
- Converters
- Recyclers
The MetaPure W-PET washing module
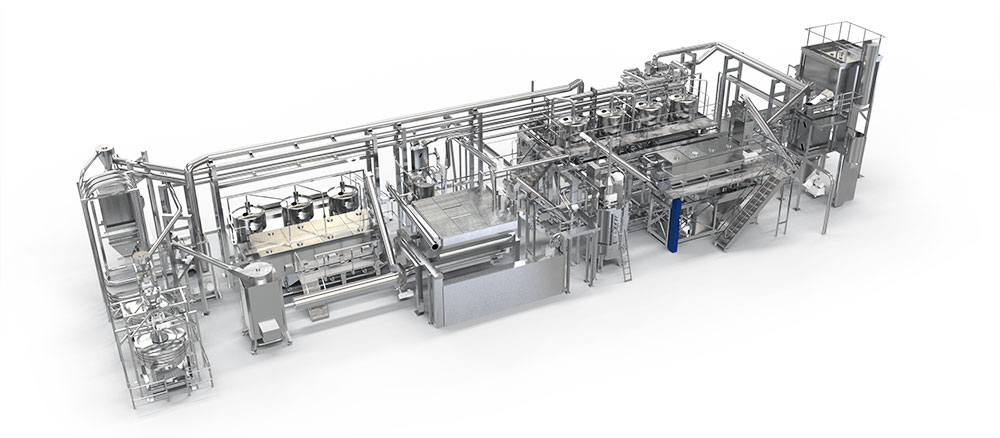
Excellent cleaning results with the Krones washing technology
- Pre-cleaning
- Caustic cleaning with caustic renewal
- Multi-stage post-washer
- Drying
- Automatic waste management system reduces the operator’s work
- Separation of labels and caps using a float-sink separation system and sifter
The Krones washing process with pre-treatment, caustic cleaning and hot post-washing ensures clean flakes with the best usability for high-quality applications (fibre, film, injection moulding).
Benefits to you with the MetaPure W-PET
- Gentle treatment of the material as the units operate with a slow rotation
- Reliable removal of dirt, organic residues and adhesives using a caustic washer
- Less cleaning and more safety for the line operators thanks to the clean design and automatic waste management system
- Possibility to reuse the process waterwith the integrated water cascade
- Very good washing results achieved with a hot post-washing process
- Reliable removal of caps and labels so that they can be reused (optional drying, separation and sack filling)
- Constant concentration and low consumption of caustic, additives and defoamers thanks to the automatic dosing equipment
- Robust construction and design of many parts in stainless steel to protect your investment
The MetaPure S decontamination module
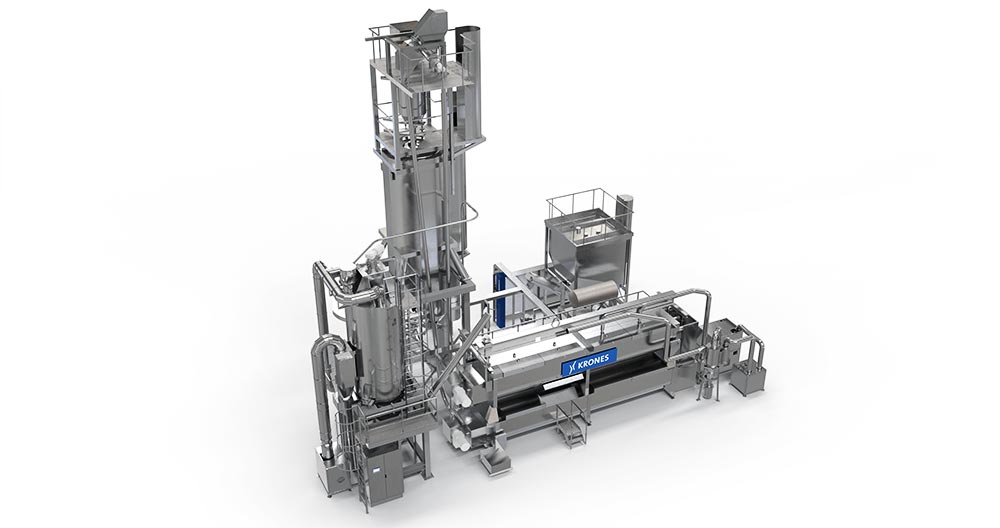
The way to food-grade flakes or pellets
- Drying and heating of the flakes
- Decontamination of the flakes to remove migrated substances
- Fixed-phase post-condensation (SSP) to raise the intrinsic viscosity (IV)
- Highest flexibility after SSP: three options for the end products
- Inline direct further processing of food-grade flakes into preforms or film possible
- Alternatively: production of pellets with double the safety by vacuum assisted extrusion (FDA) as an additional cleaning stage
Due to the fact that flakes can be decontaminated quicker than pellets, the MetaPure S stands out thanks to its lower energy requirement and gentle material handling.
Benefits to you with the MetaPure S
- Quick decontamination and IV build-up in the flake
- FDA and EFSA certificates awarded: Use of up to 100 percent rPET for food packaging
- Higher yield thanks to a vacuum reactor and heating conveyors as they generate fewer fine particles
- Energy-saving option: direct connection to machines for further processing (preform, film, fibre)
- Double the safety in the pellet process: extruder with FDA certification for extra clean pellets (optional)
- Maintenance of the vacuum system possible during operation
Our complete-system expertise – Krones as a turnkey supplier and integrator
Complete recycling plant from a single source: Factory planning, project management and recycling expertise
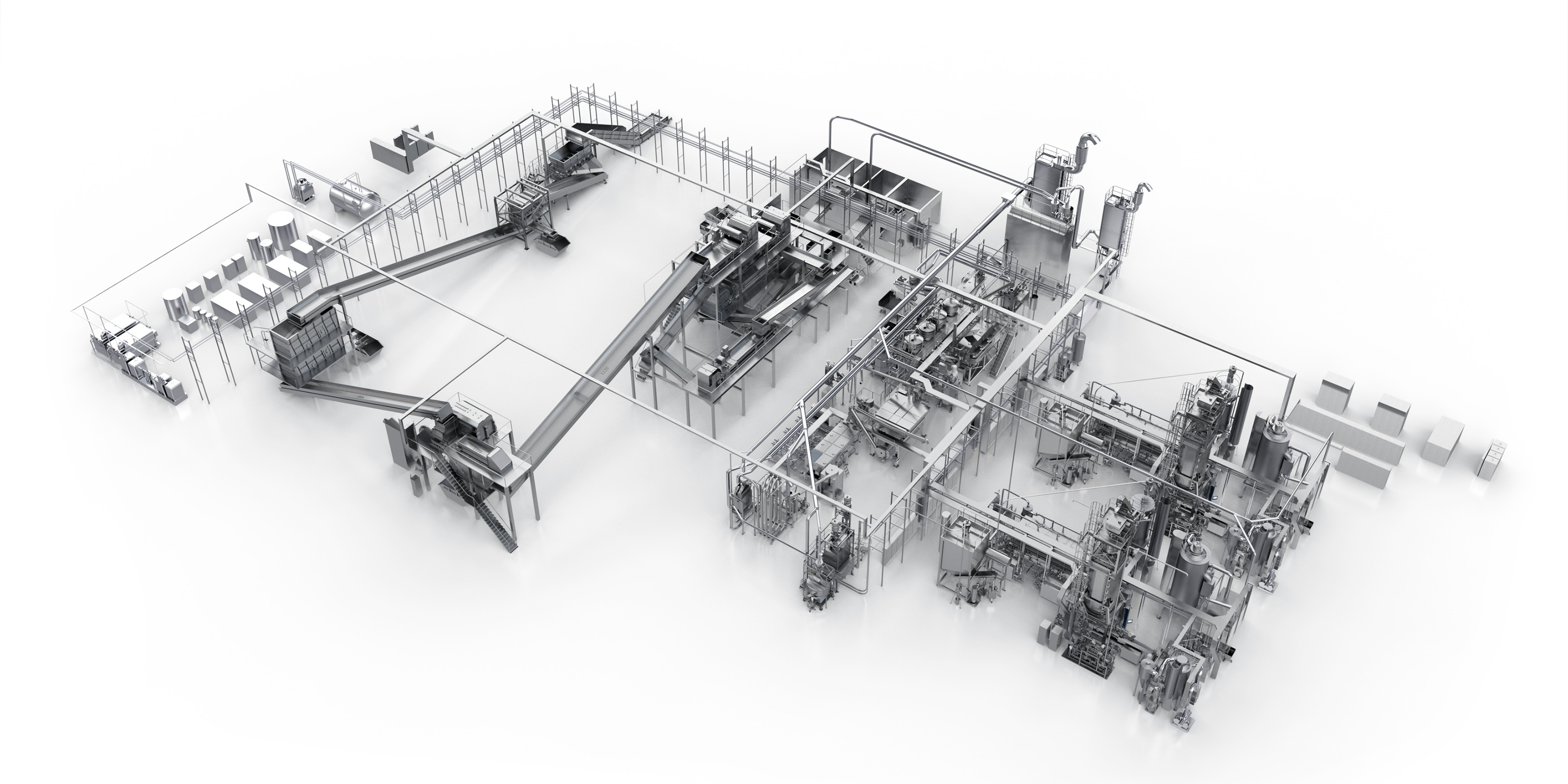
Benefits to you
- Turnkey solution from Krones: Both washing and decontamination technology from a single source
- Washing module with a well thought-out concept and excellent washing results
- Decontamination module with a unique set-up (treatment in solid and liquid phases)
- Proven technology for PET, also transferable to innovative PO recycling technology