Reliable filling of beer and flavoured beer in glass bottles
Mechanical filling system
- Reliable fill level determination via the vent tube
- End of filling after liquid contact with vent tube
- Low-oxygen filling through several pre-evacuation steps with intermediary CO2 flushing
- Electropneumatic filling valve
- One filling speed
Field of applications
- Suitable for all beer types
Output
- Up to 78,000 containers per hour
HRS = Height fillingsystem, Return gas tube, Short tube
Functional principle of the valve
First the glass bottle is pressed on and then it is pre-evacuated several times. The filling process will start as soon as the same pressure prevails in the ring bowl and the bottle. If the liquid level reaches the end of the vent tube, no more gas can escape from the bottle -and the filling valve closes. After a settling phase, the pressure in the head space of the bottle is released via the snifting valve and the filled product exits the machine.
Viscosity: < 10 mPa·s
Pulp: ≤ 0.4 mm/proportional < 10 %
Fibres: 1 x 5 mm/proportional < 5 %
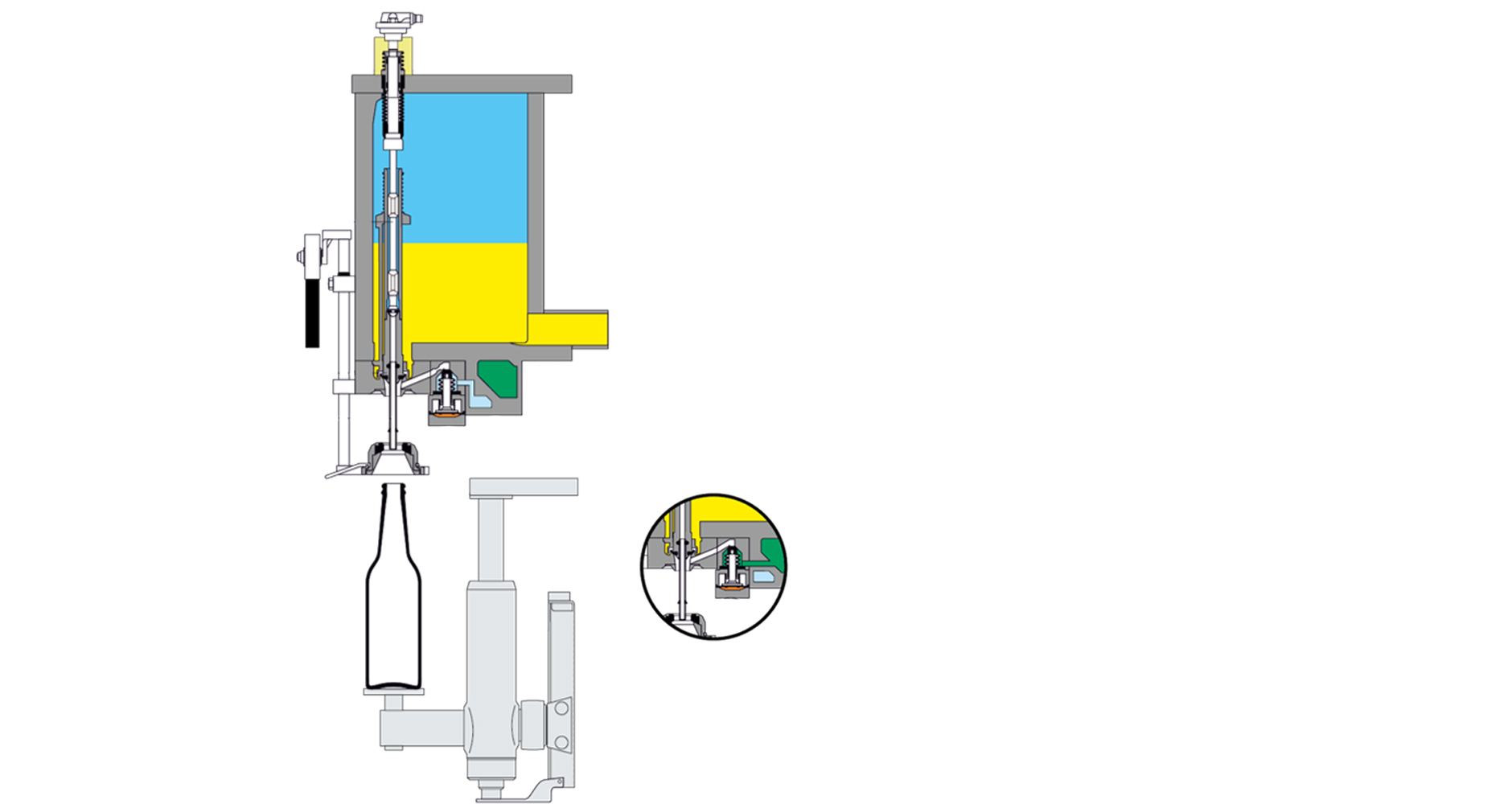
Vacuum
Snifting/CIP
Vent tube
Product stem
Gas needle
Vacuum
Snifting
Gas needle - Product stem
Benefits to You
Best technological values
- Several pre-evacuations
- Optimal interconnected CO2 flushing
Hygienic design
- Self-draining surfaces
- Clean pneumatic components hosing and electrical wiring
Precision and long service life
- Use of special pneumatic components with a significantly higher life cycle than the one of conventional switching valves
How can we help you?
Additional information
Download
Do you have any questions?
Contact
Krones nearby you
Sales network
Come and visit us
Events