Krones Inc. and its subsidiaries, such as those in Canada and Guatemala, currently employ 275 service technicians in all. And that number will continue to grow, as Krones intends to further expand its US base. David Darbant, Head of Regional Field Services at Krones Inc.’s headquarters in Franklin, Wisconsin, explains why: “Order intake is strong right now – and we’re already seeing a bottleneck in terms of service personnel to handle those orders. At the height of the pandemic, travel restrictions for some countries forced us to postpone quite a few projects. With the level of orders coming in at Krones, we can only assume that the workload will grow, not shrink,” he says, adding with emphasis that “The most important thing right now is to bring good people on board.” More service technicians in North America will not only give the site greater autonomy but also – and especially – establish a broad network of people who can be closer and more responsive to customers.
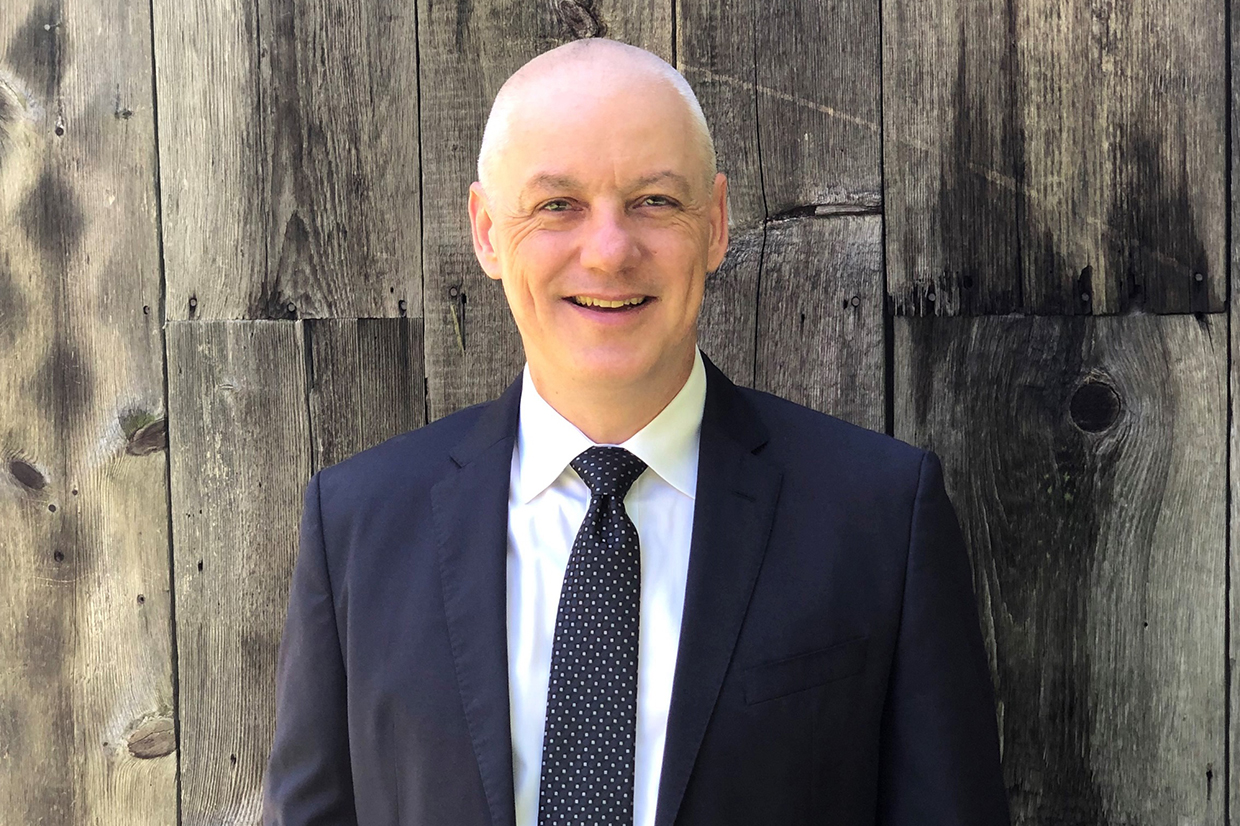