借助Contiloop AI,克朗斯为Contiform吹瓶机推出了一种智能系统:利用克朗斯智能软件和新开发硬件的组合,可以检测到PET瓶制备流程中材料分布的微小偏差,还能实时、自动调节吹瓶流程的关键参数--确保恒定的瓶子质量。
不仅设备技术,操作人员的日常工作环境也发生了变化:在灌装领域实现最先进的工艺和更高的自动化水平之后,操作人员的数量也在减少。必然结果:现在,一位操作工需要负责多台机器和系统,很少有时间查看产品质量和人工引导吹瓶机的流程。
另外,还有两个重要趋势需要关注。其一,再生PET材料(rPET)的使用,越来越多的终端消费者提出这项要求。PET瓶的优势在于符合可持续发展的要求,这意味着饮料生产商必须逐步加大再生料在瓶中的比例,最终达到百分之百使用再生PET材料。但是,不同批次的再生料之间存在差异,进而影响原料的质量和组分--这种波动的特性必须在吹瓶流程中进行补偿,因为最终每个瓶子都要满足规定的质量要求。同时,饮料生产商持续追求降低瓶子重量--不论是再生料还是新料,PET都是一种价格昂贵的原料,尤其是优质的再生料非常少见。因此,尽可能降低瓶子重量,已经成为一种必然结果--借此,节省生产流程的材料,同时进一步降低瓶子的碳足迹。
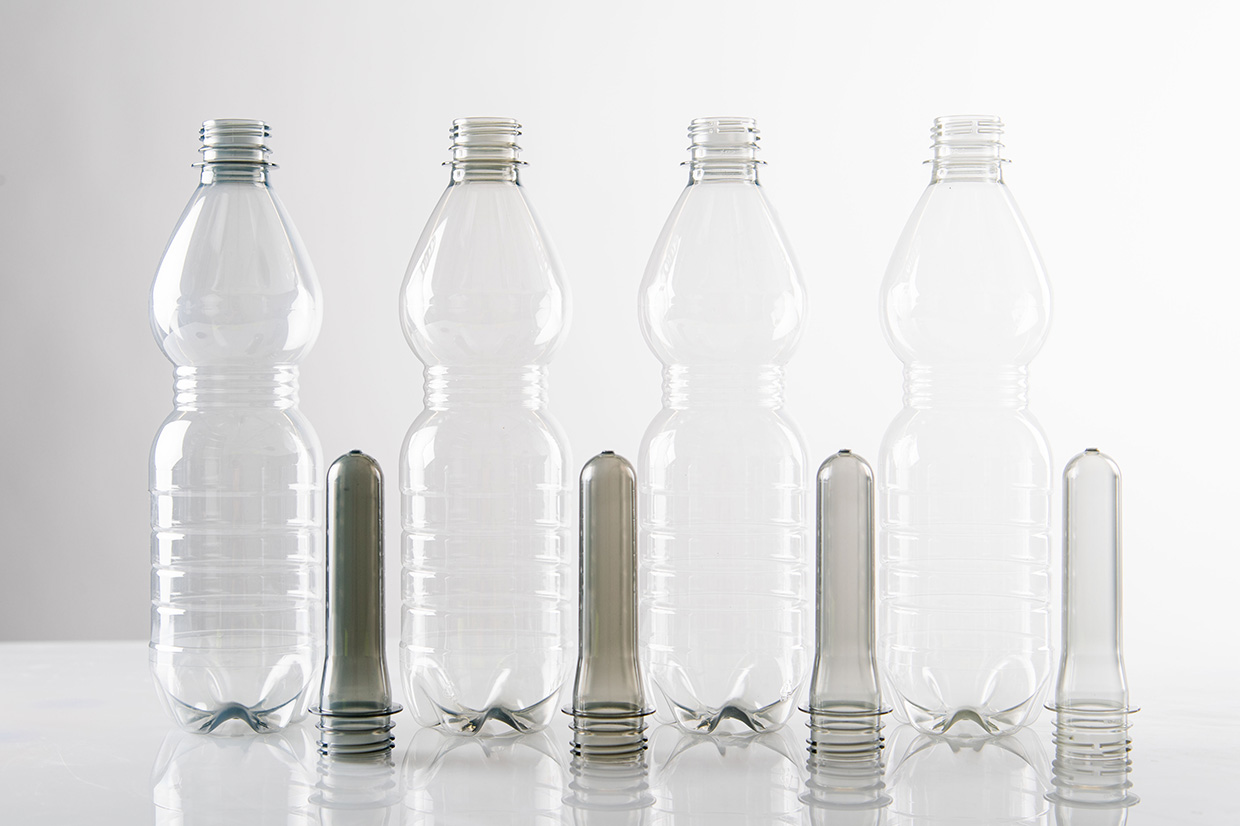
吹瓶流程的自动监视和智能控制
为了协助饮料生产商应对所有这些挑战,减少操作工的人工干预,克朗斯开发了Contiloop AI系统。
该系统完全集成在吹瓶机内,最多可以为每一个产出的瓶子在32个点测量壁厚透光度。在生产过程中,Contiloop AI可以对材料分布的微小偏差做出反应,自动、实时调整吹瓶流程。对此,还能顾及其它的基本参数,例如,环境温度,环境湿度,瓶坯的进口温度和出口温度。实施的调整显示在机器的人机界面上,操作工借此可以了解当前的流程进展情况。
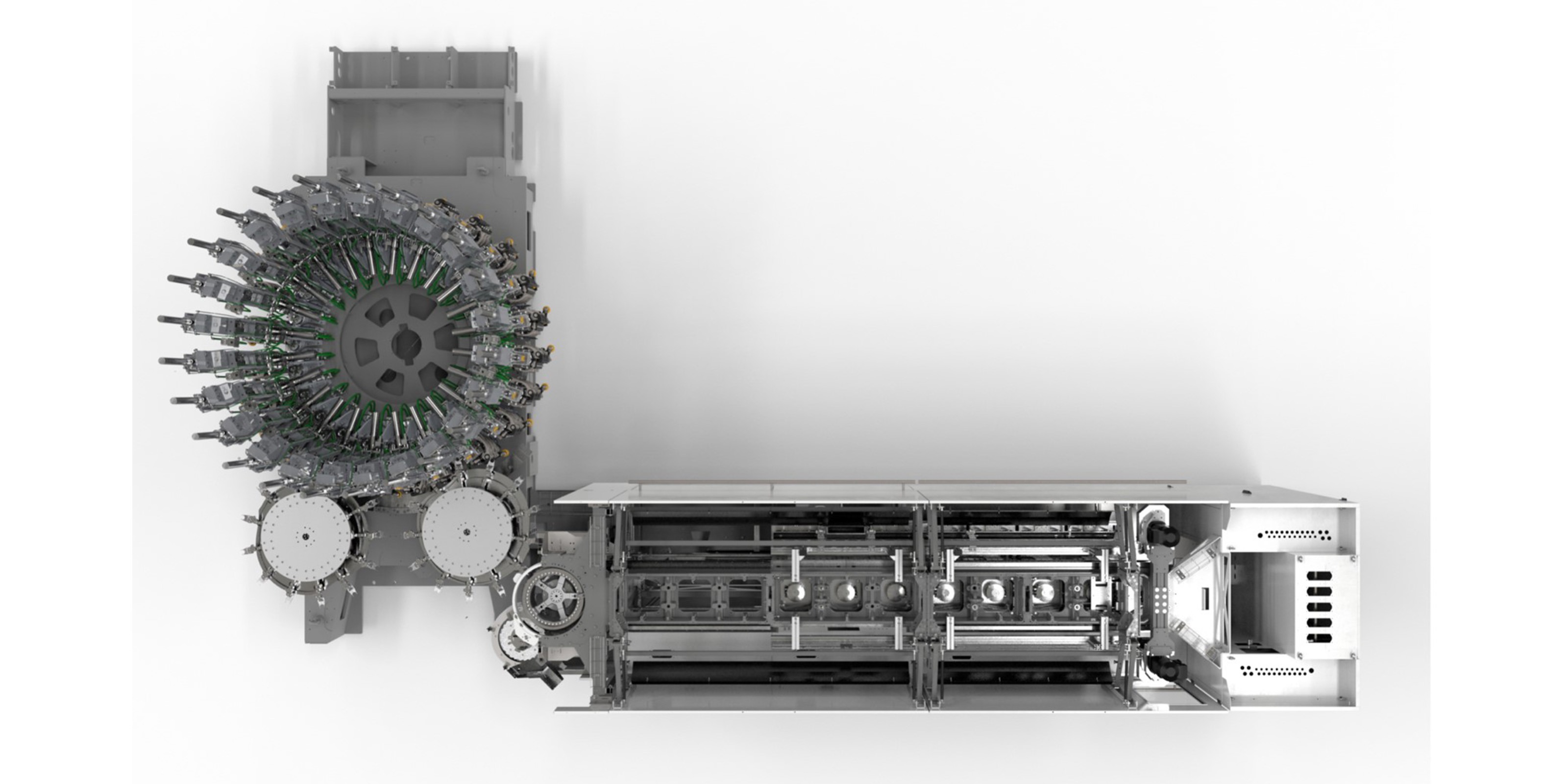
Contiloop AI 系统连接至克朗斯IIoT 平台
透光率测量桥
环境温度和空气湿度测量
预坯出料口温度测量
预坯进料口温度测量
人工智能:训练和优化系统
基于以上提到的生产运行持续改变,按照已经调好的配方进行的简单调整对于克朗斯来说是远远不够的。最初,为该系统在一次自动进行的试验流程中实施了不同的流程调整,产生的测量结果被导入克朗斯工业物联网平台。在该平台上,数据进入克朗斯智能管线,借此对今后的调节算法,即克朗斯智能体进行训练。训练结束后,将这种智能体传输给机器的Contiloop AI系统,然后提供给生产企业使用。
Contiloop AI在生产过程中的工作原理…
… 以及系统的训练和优化。
“这种系统的优势非常明显。一方面,对于今后在这台机器中生产的其它瓶型,可以为用户提供可靠、使用方便的克朗斯智能体,另一方面,还可以定期检查已经存在的智能体,如果框架条件发生较大改变,还能对其不断进行补充训练,使其更加智能”,克朗斯塑料和组合机技术产品管理负责人Robert Aust解释说。
尤其适用于再生PET材料
尤其是采用再生PET材料时,可供使用的流程窗口通常都比较小,很多情况下产生的波动都要大于新生产的PET材料。特别是生产速度快、瓶重较轻的情况下,必须非常精确地保持这条狭窄的通道。同时,还要保证非常高的瓶子质量,并将废品率降到非常低的水平。
Contiloop AI蕴藏的大量优势并非仅仅体现在材料端和流程端--它还能大幅度降低操作人员的劳动强度。一方面,通过自动化调节大量减少对机器的人工干预,另一方面,离线质量检测可以减少到最低限度。
展望未来
简化机器操作,同时保证最高的质量标准,这是克朗斯长期以来的关注焦点。今后,克朗斯将继续开发Contiloop AI系统,借助云技术和克朗斯智能扩展系统规模,帮助用户更好地应对日常生产的挑战。