Regulación inteligente de los procesos en la máquina sopladora
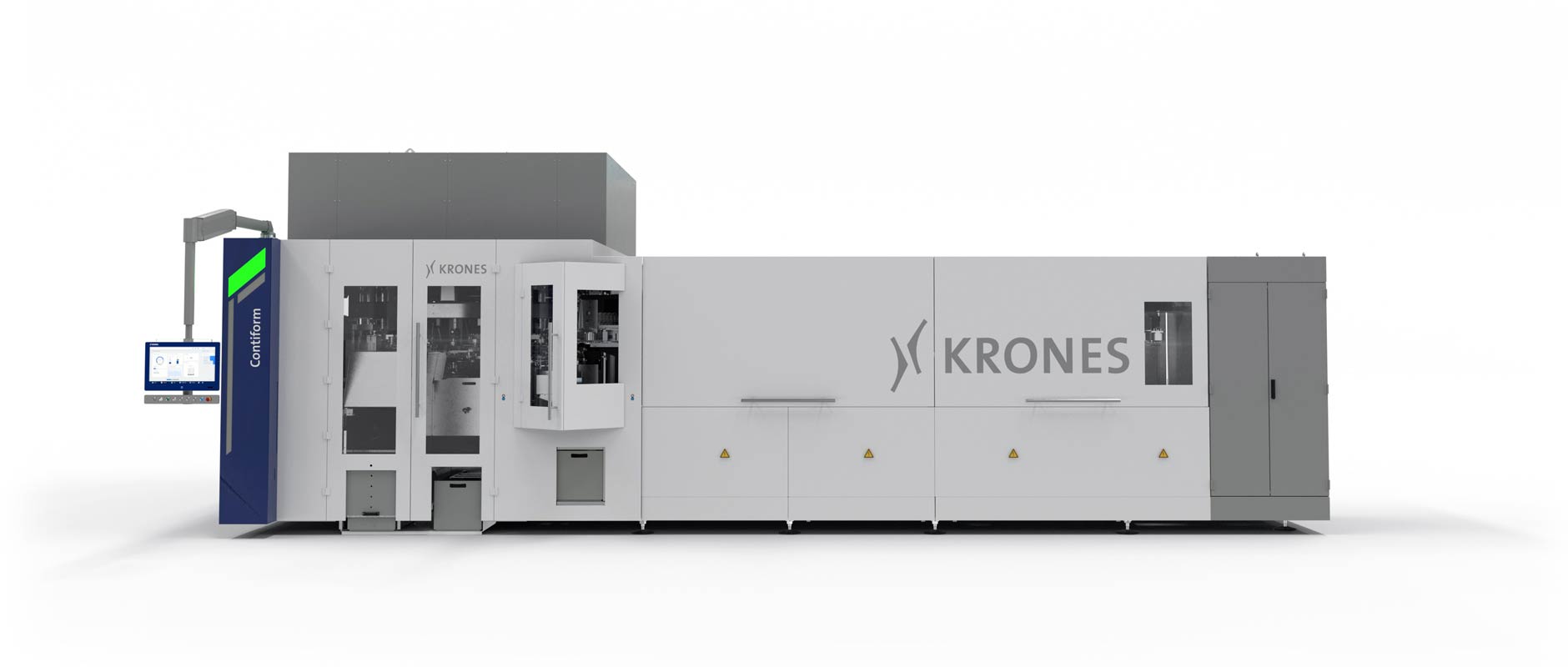
Los retos que plantea actualmente la fabricación de envases de PET son muy variados y complejos. Ya los cambios que se producen a diario en la temperatura ambiente y en la humedad del aire de la planta de producción pueden hacer necesario, con ventanas de procesamiento pequeñas, reajustar regularmente distintos parámetros del proceso a mano para asegurarse de que las botellas tienen la calidad necesaria. Otro desafío lo plantean las cifras de capacidad de producción, que aumentan constantemente: si en el año 2000 el rendimiento máximo por estación de soplado era de 1.600 envases por hora, hoy se alcanzan cifras de hasta 2.750 botellas, lo que entretanto hace posible lograr capacidades de producción de hasta 100.000 envases por hora y máquina. Por supuesto, con estas elevadas cifras ya las desviaciones más pequeñas con respecto a las condiciones ideales pueden tener un gran efecto en el resultado de la producción en un periodo de tiempo muy corto.
Sin embargo, no solo cambia la mecánica de las máquinas; también se modifica el entorno de trabajo cotidiano del personal operador: como resultado de la aplicación de la tecnología más avanzada y de un grado de automatización cada vez mayor en todos los ámbitos del llenado, se necesita menos personal que antes para garantizar el éxito de la producción. La consecuencia: en la actualidad, un operario es responsable de varias máquinas y sistemas, por lo que dispone de menos tiempo para ocuparse de los controles visuales de calidad y de la gestión manual de los procesos de la máquina sopladora.
Además, se observan otras dos tendencias determinantes. Una tiene que ver con el uso de PET reciclado (rPET), que es algo que exigen cada vez más ante todo los consumidores finales. Para los productores de bebidas, combinar las ventajas de los envases de PET con la sostenibilidad significa acercarse paso a paso a aumentar el porcentaje de rPET presente en las botellas a hasta el 100 %. Pero no todos los rPET son iguales: la calidad y la composición del material varían. Y son precisamente estas características cambiantes las que se deben compensar durante el proceso de estirado-soplado, para que al final cada uno de los envases producidos reúna los requisitos de calidad establecidos. Al mismo tiempo, los productores de bebidas siguen intentando reducir el peso de los envases. Porque el PET, reciclado o nuevo, es un material caro, y especialmente el rPET de alta calidad es escaso. Por eso, es lógico que se intente disminuir al máximo el peso, para ahorrar material en el proceso de producción y para seguir reduciendo la "huella de carbono" de los envases.
Monitorización automática y control inteligente del proceso de estirado-soplado
Para ayudar a los productores de bebidas a superar todos estos retos y para que puedan prescindir de los pasos de manejo manuales, Krones ha desarrollado el Contiloop AI.
Completamente integrado en la máquina sopladora, el sistema mide el grado de transmisión de la luz de cada uno de los envases producidos en hasta 32 puntos de medición. Durante la producción, el Contiloop AI reacciona incluso a las desviaciones más pequeñas en la distribución de material, y reajusta automáticamente y en tiempo real el proceso de estirado-soplado. Para ello se tienen en cuenta también otros parámetros, como la temperatura ambiente y la humedad del aire, así como la temperatura de entrada y salida de la preforma. Las adaptaciones que se llevan a cabo se muestran en la interfaz humano-máquina, para que el operador pueda tener siempre una visión general de la gestión actual del proceso.
Gracias a la inteligencia artificial: el sistema se puede entrenar y optimizar
Y, sin embargo, dados los cambios constantes en la producción ya mencionados, una simple regulación basada en una fórmula ajustada una vez no es suficiente para Krones. En un inicio, se configuran para el sistema, durante una marcha de prueba automática, distintos ajustes de proceso, y se envían los resultados de medición que se obtengan a la plataforma de IIoT de Krones (IIoT: Industrial Internet of Things). Allí, los datos entran a formar parte de los recursos de IA de Krones, con lo que se entrena el futuro algoritmo de regulación, el agente IA. Una vez completado este entrenamiento, este agente IA se envía al Contiloop AI de la máquina, y queda disponible para la producción.
Especialmente rentable cuando se usa rPET
Sobre todo cuando se usa rPET, la ventana de procesamiento disponible suele ser muy pequeña, y, en algunas circunstancias, varía más que cuando se utiliza PET nuevo. Este pequeño intervalo se respeta con gran precisión incluso con una capacidad de producción elevada y con envases de peso reducido. Al mismo tiempo, el Contiloop AI garantiza que se obtienen envases de una calidad muy alta y que la tasa de piezas defectuosas (tasa de rechazo) se puede mantener a un nivel muy bajo.
Pero las numerosas ventajas del Contiloop AI no se reducen solo a los ámbitos del material y de los procesos: también se simplifica de forma determinante el trabajo del personal operador. Por un lado, la regulación automática reduce enormemente la necesidad de intervenir manualmente en la máquina. Por otro, también se puede reducir a un mínimo el control de calidad offline.
Descargas
